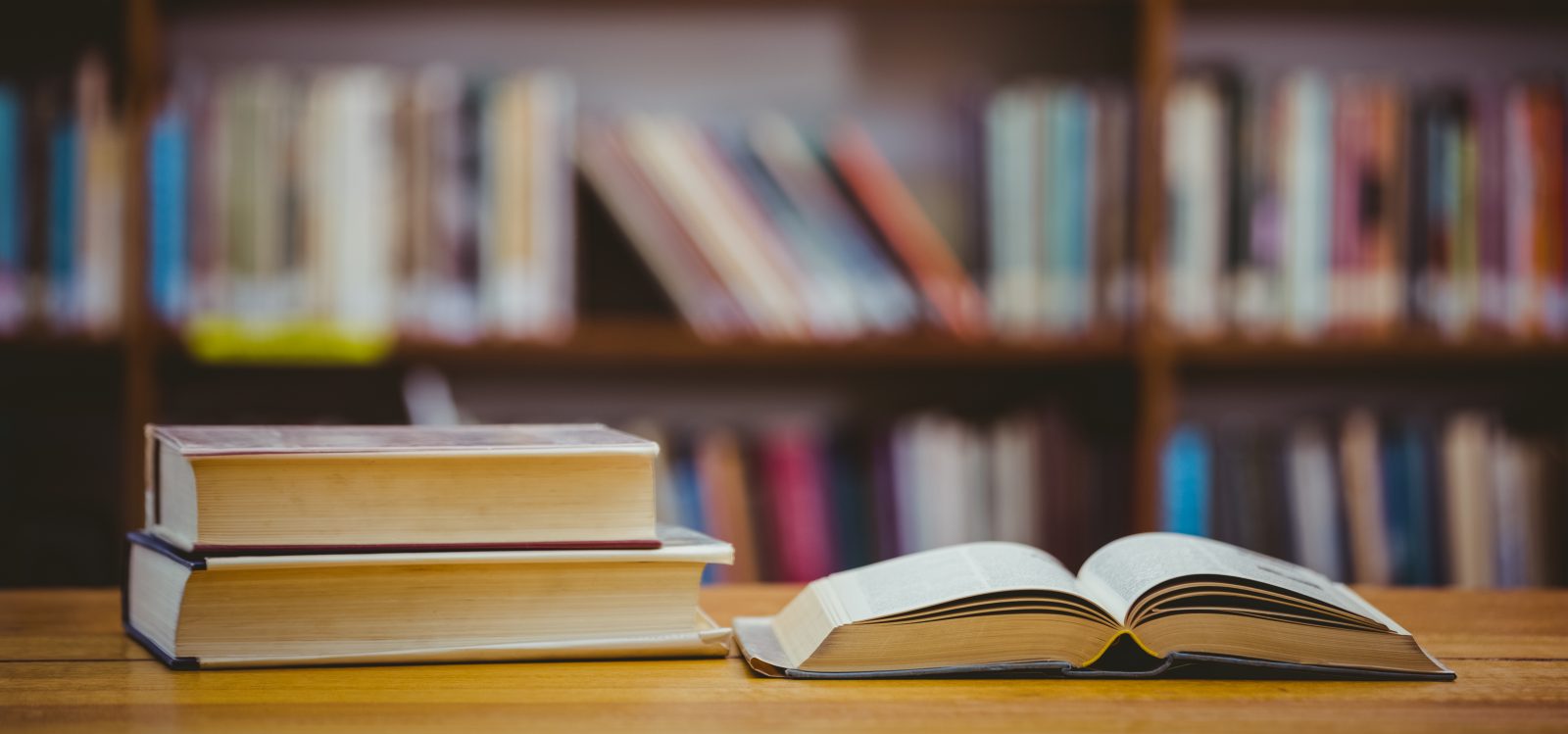
CHAPTER 1 INTRODUCTION 1. HISTORY AND GENERAL INFORMATION ON ADIPIC ACID 1. History on The Production Adipic acid is an important organic chemical raw material. In China, it is used as raw material in the production of Nylon 6/6 salt, polyurethane, plasticizers, high-grade lubricants and food additives. With the rapid growth of development, the application of adipic acid keeps expanding. The production of adipic acid is controlled in the hands of multinationals. An American chemical company (DuPont) is the biggest supplier in the world.
On 2004, total capacity of adipic acid in the world was recorded to be as much as 2. 74 million tons and Du Pont alone caters about 1. 1 million tons which is almost 38% of the world total. After experiencing a period of rapid growth on the 80s, adipic acid production entered a period of stable growth in the 1990s. It is expected that the capacity of adipic acid will still maintain an annual growth of over 3% in the next few years (China National Chemical Information Center Reproduced, 2007). China produced approximately 200 000 tonnes per annum.
Over 45 300 tons of adipic acid was produced in 2000, but increased to 70 100 tonnes in 2001 and 133 400 tonnes in 2003 and the import amount in 2004 reached 173 700 tonnes, an increase of 30. 2% over 2003. The import amount of adipic acid has increased at an annual rate of over 30% for four consecutive years and the dependence on import has reached more than 50% (Xudong Zhang, 2005). Due to the high demand on import, the market price of adipic acid has started at a very high rate. In the years after 2001 the price of imported adipic acid was maintained at RMB 9 000-11 000 per ton in the domestic market.
The price of domestic adipic acid was fixed according to the price of imported goods and was therefore basically similar with the import price. However in 2004, due to the oil price rise in the international market, the price of raw materials for the adipic acid production has made a drastic increase. The demand of adipic acid therefore made a rapid increase and the price also had a drastic rise. The price of adipic acid rises up to RMB 15 500 per ton in November 2004, hitting historical high.
Even though the oil price in the international market dropped in early December 2004, the price of adipic acid still remained at a very high level amount (China National Chemical Information Center Reproduced, 2007). [pic] Figure 1. 1: 2003 adipic acid productions According to a pie chart in figure 1. 1, United States is the leader of the production of adipic acid with 36%, followed by Germany with 14%, France (11%), United Kingdom (8%), Canada (6%), South Korea and China both with 5%, Japan and Singapore with 4%, Brazil (3%) and lastly Italy and Ukraine with 2% each.
Adipic acid is mainly use as monomer in manufacture Nylon 6/6 fiber, plasticizer, grease, polyurethane etc. There are several countries in the world that manufacturing the adipic acid. But there also countries that just is a supplier for this adipic acid to any factory that need adipic acid in their countries. The main countries that produce adipic acid are United State of America and also China. Almost ninety percent of adipic acid manufactured in United State of America is used to produce Nylon 6/6 fiber. In America also there is four adipic acid manufacturing plant in operation which are: Allied Signal Inc. which situated in Hopewell, Virginia with annual production capacity of 15,000 tonnes per annum. ? DuPont Chemicals in Orange, Texas producing about 190,000 tonnes per annum. ? DuPont Chemicals in Victoria, Texas producing 350,000 tonnes per annum. ? Monsanto Chemical Company in Pensacola, Florida with annual production capacity of 300,000 tons per annum. In China also there are several major companies that manufacturing adipic acid. Products produced are use to export and commercial use in their own country.
In China, local manufacturers opened more than one factory locally and international such as Rhodia of France and BASF of Germany. Currently in Malaysia, it is not producing or manufacturing any adipic acid but they only become the supplier for the local industries. For this matter, Malaysia should build at least one manufacturer plant of adipic acid to decrease the import of the adipic acid from other countries. There are not many adipic acid plants in the world and therefore local manufacturer should grab this opportunity and not just depending on outside sources.
This would make Malaysia one of the largest productions of adipic acid in the world. 2. General Description Generally, adipic acid has a structure of Carbon 6 straight-chain with two carboxylic acid (-COOH) groups. Due to its long aliphatic chain, it is slightly soluble in water, alcohol and acetone. Adipic acid can also be called as 1,4-butanedicarboxylic acid, 1,6-hexanedioic acid, adipinic acid, acifloctin, acinetten, octafluorohexanedioic acid as well as hexanedioic acid.
It is expected to have a chemical formula of C6H10O4 and a structural formula of HOOC(CH2)4COOH with a total molecular weight of 146. 14 gmol-1. Figure 1. 2 is the structures of adipic acid: Figure 1. 2: Molecular structure of adipic acid Commercial adipic acid is one of the purest chemicals produced on a large scale (99. 8%) because of the extreme sensitivity of polyamide synthesis to impurities. Typical impurities include other acids such as monobasic acids and lower dibasic acids, nitrogenous materials, trace metals such as iron, heavy metals, and arsenic and hydrocarbon oil.
Since the material is odorless and irritant properties are unreliable, therefore it can be assumed that the warning properties are poor (PubChem Public Chemical Database, 2008). Adipic acid consumption is linked almost 90% to nylon production by the polycondensation with hexamethylenediamine. Adipic acid is used in manufacturing plasticizers and lubricants components. It is used in making polyester polyols for polyurethane systems. Food grade adipic acid is used as gelling aid, acidulant, leavening and buffering agent.
Adipic acid has two carboxylic acid, -COOH groups, which can yield two kinds of salts. Its derivatives, acyl halides, anhydrides, esters, amides and nitriles, are used in making target products such as flavoring agents, internal plasticizers, pesticides, dyes, textile treatment agents, fungicides, and pharmaceuticals through further reactions of substitution, catalytic reduction, metal hydride reduction, diborane reduction, ketone formation with organometallic reagents, electrophile bonding at oxygen, and condensation (SIDS, 2004). 2. PHYSICAL AND CHEMICAL PROPERTIES Table 1. : Physical and chemical properties of adipic acid |Property |Description | |Physical State |Crystalline Powder | |Appearance |White | |Crystal System |Monoclinic | |Odor |Odorless | |Melting Temperature |152 – 154 (oC) | |Boiling Temperature |337 (oC) | |Decomposition Temperature |315 (oC) | |Flash Temperature |210 (oC) | |Specific Gravity |1. 36 | |pH |3. 5 | |Solubility in Water |Slightly Soluble | |Autoignition |420 (oC) | |Vapor Density |5 ([pic]) | |Stability |Stable under ordinary conditions | |Refractive Index NFPA Ratings |Health: 1, Flammability: 1, | | |Reactivity: 0 | |Vapor Density |5 | |Toxicity |Oral rat LD50: >11 gm/kg | Source: Polytrans S. A, 2005 3. USAGE OF ADIPIC ACID Adipic acid is a very important chemical that is used all over the world to produce various products that people use every day. Nylon 6/6, foams, paints and tires are just a few of the products that are formed by using adipic acid.
Adipic acid is also used as a food ingredient in gelatins, desserts and other foods that require acidulation. Nylon 6/6 is the largest outlet for adipic acid, accounting for more than 89% of the total consumption in North America. One of the leading producers, BASF, produces about 31,752 metric tonnes of nylon per year. Nylon is used for everyday applications such as electrical connectors, cable tires, fishing line, fabrics, carpeting, and many other useful products. Figure 1. 3 that the consumption and production for adipic acid is dominated by the United States. Out of 2. 3 million metric tonnes of adipic acid produced worldwide, 42% is produced in the United State while the United State consumes 62% of total production.
Western Europe produces the majority of the remaining adipic acid with 40%, and 13% in Asia-Pacific, while the other regions account for the remaining 5% (Anne Gerasi, 2007). [pic] Figure 1. 3: The worldwide production of adipic acid By far the main use of adipic acid is as monomer for the production of nylon by a polycondensation reaction with hexamethylene diamine forming Nylon 6/6. Other uses include: • Monomer for production of Polyurethane • reactant to form plasticizers and lubricant components • Food ingredient as a flavorant and gelling aid. [pic] Plate 1. 1: The product of crystalline adipic acid 1. Usage in The Production of Nylon Adipic acid consumption is linked almost 90% into the production of nylon through polycondensation which then produce Nylon 6/6.
Nylon, having a protein-like structure, which will be further processed into fibers for applications in carpeting, automobile tire cord and clothing. Based on the global demand for nylon resins, which is used especially in engineering plastics, the usage of adipic acid has grown from 8 to 10 percent per year during the past decade (Anastas and Warner, 2008). The market for Nylon 6/6 is predominantly in fibers, while high-specification Nylon 6/6 resin, with or without fillers or modifiers. Adipic acid and Nylon 6/6 supply in North America, Western Europe, and Japan is dominated by DuPont, BASF, Monsanto, Rhone-Poulenc, Asahi Chemical, Bayer, and AlliedSignal. The technologies for adipic acid and Nylon 6/6 production are closely held by those companies (Anne Gerasi, 2007).
Nylons are among one of the most important commercial polymers (large molecules) made up of many covalently-linked smaller molecules (monomers). A monomer is a molecular building block that can be used to make up a polymer chain when bond together with other monomers. Since Nylon 6/6 is made up from two different monomer of adipic acid and 1,6-diaminohexane, it is called a copolymer. Figure 1. 4 shows how the reaction between those two reactants reacts to produce nylon. [pic] Figure 1. 4: The kinetic reaction to produce Nylon 6/6 2. Usage in Food Industry Food grade adipic acid is used as gelling aid, acidulant, leavening and buffering agent (plate 1. 2).
It is also used in gelatins to promote rapid setting, provide tartness and protect against quality loss. It is also used in beverages, condiments, relishes, dairy product analogs, fats and oils, frozen dairy desserts, puddings, gravies, meat products and snack foods. Since it is nontoxic, therefore most of the food that contains this adipic acid is suitable for people following Kosher, halal, and vegetarian diets (Werpy et al, 2004). Adipic acid and food industry links with each other in a very close need bonding. It can be found that many of the foods contain a chemical compounds which include adipic acid and it can be prove by finding them on the ingredient labels.
Some are naturally occurring compounds, others are chemically synthesized, and all work done by this chemical compounds are to (theoretically) improve the quality of foods (New Jersey Department of Health and Senior Services, 2004). [pic] Plate 1. 2: Foods that contain adipic acid 3. Other Applications Other major volume uses are in the preparation of esters for use as plasticisers and lubricants identified by names ending in “adipate” (a salt of adipic acid) and are used as a chemical intermediates across a very wide range of industries. The most common products are di-octyl adipate (DOA), di-methyl adipate (DMA) which are used in processing other polymers, solvents, special lubricants, aircraft lubricants, cosmetics, rubber industry etc. It is also used in the manufacture of water treatment products with purpose to treat and clean the water.
Examples of a substance are flocculants, chlorine purification and domestic clean (Valetime group website, 2009). Technical grade adipic acid is used to make plasticizers, adds flexibility and resilience to unsaturated polyesters, is used in the production of rigid and flexible foams, wire coatings, elastomers, and adhesives, increases flexibility of alkyd resins, is used in the production of wet strength resins for the paper chemicals industry and is used in the production of synthetic lubricants components and greases. Plasticizers and lubricants components are used in making polyester polyols for polyurethane systems (Jennifer Petru, 2001). Adipic acid has two carboxylic acid, -COOH, groups, which can yield two kinds of salts.
Its derivatives, acyl halides, anhydrides, esters, amides and nitriles, are used in making target products such as flavoring agents, internal plasticizers, pesticides, dyes, textile treatment agents, fungicides, and pharmaceuticals through further reactions of substitution, catalytic reduction, metal hydride reduction, diborane reduction, ketone formation with organometallic reagents, electrophile bonding at oxygen, and condensation (Werpy et al, 2004). CHAPTER 2 PROCESS BACKGROUND 1. THE PROCESSES Basically, there are three famous processes used in the production of adipic acid. They are the production from cyclohexane using catalyst, phenol and benzene via cyclohexene process.
Even though these three routes have very different characteristics and cost distributions, ranging from the high raw material costs but comparatively low capital costs for the phenol-based route. Figure 2. 1 represent all kind of processes involves in order to produce adipic acid. Three routes of processes are shown in that figure which are commercially used in today’s life, has been in commercial used as well as the route that has been demonstrated but not in commercial use. [pic] Figure 2. 1: Adipic acid processes: ( ) in commercial use today, ( ) has been in commercial used, and (- – -) demonstrated but not in commercial use. 1. Production of Adipic Acid from Cyclohexane
Adipic acid is one of the dicarboxylic acids where back before the technology was enhanced, the adipic acid was produced from various fats using oxidation method. But today after undergo many years of achieving technology, the adipic acid is produced from cyclohexane by two oxidation steps. Typically, it is a white crystal solid which is soluble in alcohol and acetone. Major uses for the adipic acid are for producing Nylon 6/6 fiber and plastics. Another use of the adipic acid is on ester used for plasticizer and lubricants. There is some consuming the acid used as food acidulants. In such a way, when cyclohexane reacts with excess oxygen in the air the result will be cyclohexanol and cyclohexanone plus some other byproducts.
This cyclohexanol-cyclohexanone mixture is also known as ketone–alcohol or KA mixture. After that, the KA mixture will be catalytically oxidized using nitric acid to produce the adipic acid and also the nitrous oxide. There are several catalysts that been use to promote the reaction such as cobalt catalyzed oxidation and borate promoted oxidation (Cary, 1992). Without exception, currently operating commercial production processes for adipic acid depend on the production or purchase of KA Oil or of pure cyclohexanol and its subsequent oxidation in solution to adipic acid using an excess of strong nitric acid. The most common route to the KA Oil needed for adipic acid production is the excess air oxidation of cyclohexane.
Most commercial routes combine hydroperoxide formation and decomposition in the presence of a catalyst, most commonly low concentrations of cobalt sometimes combined with other metals. An alternative commercial established route uses substantial quantities of recycled boric acid as a catalyst, which also forms an ester with the cyclohexanol as it is formed (J. M. Rung, 1992). The second step in producing the adipic acid after produced both cyclohexanol and cyclohexanone is by oxidation the mixture with nitric acid. To promote the reaction of the second step of producing the adipic acid is by using a copper–vanadium catalyst with the nitric acid. All reactants are fed into either a multiple-stage column reactor or a series of plug flow reactors, with a low conversion rate from feedstock to oxidized product.
This low rate of conversion necessitates effective recovery. Usually nitric acid will be use as much as 60 percent out of the reactants. The reactants and catalyst will both react in the reactor vessel up to temperature of 160oC to 260oC with the pressure of 0. 1 MPa to 0. 4 MPa. As chemical reaction applied, the conversion yield will be increase as much as 96 percent attainable when using high purity KA mixture feed. KA oil oxidizes effectively with 55 to 65 percent nitric acid in the presence of copper and vanadium catalysts. This results in a very high yield of adipic acid. The reaction is exothermic, and can reach an autocatalytic runaway state if temperatures exceed 280°C.
Process control is achieved by using large amounts of nitric acid (Bayer Polymers, 2003). Nitrogen oxides are removed by bleaching with air, water is removed by vacuum distillation, and the adipic acid is separated from the nitric acid and KA mixture by distillation column. Liquid adipic acid is crystallized by crystallizer. Further refining, typically recrystallization from water is needed to achieve polymer-grade material. Every common reaction will have its own byproducts same goes to the process production of adipic acid. Upon reaction, nitric acid will reduces to become NOx such as nitrogen dioxide (NO2), nitrogen oxide (NO), nitrous oxide (N2O) and also nitrogen (N2).
These byproducts cannot just be purging out from the plant without treat it because some of the byproducts are hazardous to life and also to the environment (Swiss Product Register, 2003). The dissolved oxides will strip from the reaction product using air in bleaching column before it can be recovered back as nitric acid in an absorption column. The wet adipic acid crystals are separated from water. The product is then dried and cooled before being pack and ship for sale. Dibasic acids (DBA) may be recovered from the nitric acid solution and can be sold as a byproduct. The remaining nitric acid is then recycled back to the second reactor to minimize the operating cost (Bayer Polymers, 2003). 1. Emissions and Control
Organic compound and carbon monoxide (CO) from the first reaction were the primary emission from the manufacture of production adipic acid consist, NOx from the second reaction, and particulate matter from cooling products, drying, storage, and loading. Carbon monoxide (CO), and carbon dioxide (CO2) and would contain as waste gas stream of cyclohexane oxidation, after removal most of valuable unreacted cyclohexane. In addition, it will contain metals, residue from catalyst, and volatile and nonvolatile organic compounds from the final distillation column (“nonvolatile residue”). The spent caustic waste can be burned or sold as a recovered byproduct.
Cyclohexanone, cyclohexanol, and hexanol are among the organic compounds emitted from the cyclohexane recovery equipment but hexanol can be assumed negligible since the composition is very small (decanters and distillation columns) (Ashford’s Dictionary of Industrial Chemicals, 2001). The results of the KA’s in 2 main streams were the result from Nitric acid oxidation. It is contains primarily water, nitric acid, and adipic acid as the liquid effluent, contains significant quantities of NOx, which are considered part of the process stream with recoverable economic value. The gaseous effluent from oxidation contains NOx, CO2, CO, nitrous oxide (N2O), and DBAs. To recover most of the NOx, the gaseous effluent from both the bleacher and the oxidation reactor typically is passed through an absorption tower, but this process does not significantly reduce the concentration of N2O in the stream.
The absorber off gases and the fumes from tanks storing solutions high in nitric acid content are controlled by extended absorption of the plants utilizing cyclohexane oxidation, and by thermal reduction at the remaining. The volume of the absorber should be increased to accomplish the extended absorption, by extending the residence time of the NOx laden gases with the absorbing water, and by providing sufficient cooling to remove the heat released by the absorption process. It is less economical if the thermal reduction involves reacting NOx with excess fuel in a reducing atmosphere than extended absorption (Official Emission Declaration, 2002).
The adipic acid dust particulate emissions from product drying, cooling, storage, and loading operations should be control. Both scrubbers and bag filters are used commonly to control it. Nitric acid emissions occur from the product blowers and from the centrifuges and filters used to recover adipic acid crystals from the effluent stream leaving the second reactor. However, all of it can be assumed to be emitted to the atmosphere when chlorine is added to product cooling towers. Methanol emission will also occur if DBA are recovered of nitric acid solution and convert to dibasic esters (DBE) using methanol but since the amount of methanol produces is small it can be assume negligible (Process Economics Program Yearbook, 2002). 2.
Production of Adipic Acid from Phenol Another method to producing adipic acid which is unfamiliar and lesser used in the commercial usage is the phenol hydrogenation. First step is by molten the phenol through hydrogenation at temperature of 140oC or 284oF. The pressure that usually use is between 200 kPa to 1800 kPa or 2 atm to 18 atm. This hydrogenation will be using catalyst to promote the reaction rate. There are some catalyst that been use such as nickel, copper or chromium oxide catalyst (PERP Program, 1999). These catalysts are predominantly produced or yield the cyclohexanol which is one of the reactants for production of adipic acid.
Another reactant which is cyclohexanone, is an intermediate product in manufacturing of caprolactam which usually using a palladium catalyst in the process (U. S. Environmental Protection Agency, 1991). The second step in producing the adipic acid after produced both cyclohexanol and cyclohexanone is by oxidation the mixture with nitric acid. Both cyclohexanol and cyclohexanone will react with nitric acid to produce adipic acid. The reaction actually is a highly exothermic reaction which will release energy in a form of heat at high rate. The heat reaction is usually dissipated by using and maintaining the high ratio of nitric acid to KA mixture. The common value for the ratio is 40:1 (Gale Group of a Thomson Corporation Company, 2007).
To promote the reaction of the second step of producing the adipic acid is by using a copper – vanadium catalyst with the nitric acid. Usually nitric acid will be use as much as 60 percent out of the reactants. The reactants and catalyst will both react in the reactor vessel up to temperature of 160oC to 260oC with the pressure of 0. 1 MPa to 0. 4 MPa. As chemical reaction applied, the conversion yield will be increase as much as 96 percent attainable when using high purity KA mixture feed (Adipic Acid, 1994). Every common reaction will have its byproducts same goes to the process production of adipic acid. Upon reaction, nitric acid will reduces to become NOx such as nitrogen dioxide, nitrogen oxide, nitrous oxide and also nitrogen.
These byproducts cannot just be purging out from the plant without treat it because some of the byproducts are hazardous to life and also to the environment. The dissolved oxides will strip from the reaction product using air in bleaching column before it can be recovered back as nitric acid in an absorption column. The stripped adipic acid will be brought to the next process which is crystallization process where the adipic acid will be chilled to form crystals of adipic acid. The crystals will be separated from the unconverged solution which called mother liquor in a centrifuge and will be transport to the adipic acid drying and/or melting facilities according to the customer wanted before it goes for storage.
The mother liquor will be separated from the uncrystallized adipic acid where the mother liquor will be recycle back to the reactor to prevent wasting and to promote the purity of the apidic acid and uncrystallized adipic acid will be chilled to crystallized it (PERP Program, 1999). 3. Production of Adipic Acid from benzene A company of Solutia which worked together with the Boreskov Institute of Catalysis (BIC) in Russia, has developed a one step process to manufacture phenol from benzene, using nitrous oxide for the oxidation step. Figure 2. 2 is the simplified version of the process. Thus, by coupling phenol production and adipic acid production, Solutia has no net production of nitrous oxide and very good production economics for both phenol and adipic acid (Paster. et al, 2003).
The combination of aqueous hydrogen peroxide and a molecular sieve catalyst allows slow oxidation of cyclohexane to adipic acid in the absence of organic solvent. The mechanism is via cyclohexane oxide and cyclohexanediols but more than one mechanism may operate. 100% conversion can be achieved at 80oC for 72 hrs with a turnover number of 310, but as yet selectivity is 30% (Kazuhiko Sato et al, 2005). The industry developed a practical oxidation method with aqueous 30% H2O2 as a phasetransfer catalyst (PTC). This aqueous, organic biphasic reaction enables the high yield epoxidation of olefins, as well as the oxidation of primary and secondary alcohols under conditions that are entirely free of organic solvents and halides.
The high catalytic efficiency can be obtained only by using a quaternary ammonium hydrogensulfate. When a mixture of cyclohexene was stirred in air at 1000 rpm and at a temperature of 75°C to 90°C for 8 hours, an adipic acid was formed in 93% yield. The percentage yield can be check using gas chromatographic (GC) analysis (Kazuhiko Sato et al, 2005). [pic] (a) [pic] (b) a) represent the general reaction b) represent thee more complete reaction Figure 2. 2: Summarize of the complete reaction using benzene via cyclohexene process. 2. PROCESS SELECTION 1. Process Chosen The production of adipic acid from cyclohexane through two oxidation processes is chosen. All processes proposed in section 2. are unique and interesting to look at but the production using cyclohexane as a raw material has its own uniqueness which automatically attracts the group attention. 2. Selection Criterion The selected process is chosen base on a few factors. The most important factor is to limit the production and operation cost. When compared the price of the raw materials of all processes, the most expensive raw materials is phenol, followed by benzene then later is cyclohexane. Even though the cheapest raw material is chosen, the percentage conversion is still similar with those in benzene and phenol. Since the price of adipic acid is high, short years is needed to achieve break–even market (Aromatics Market Reports, 2005). Production from cyclohexane only needed two reactions processes to produce adipic acid.
Less process reaction means fewer reactors is needed and therefore will lower the operation cost. Apart from that, any process involving reactors are difficult to run since it only operates at a certain high temperature or pressure and even sometimes it needs both. Since most reactors are highly expensive and sensitive, it is advised to limit the usage of reactor. This limitation acts as the most important criteria in choosing the best process. Most company uses processing of adipic acid through cyclohexane. This does mean that it is the most commercial process used in industries these days. This type of process has been established for many years.
DuPont is the creator of this process. Many researches are still being done in improvising phenol and benzene processes. Furthermore, the supply of nitric acid as use in second oxidation can easily been found in Malaysia. In other way, it will cut off some of the expenses for raw materials transportation. As the price for cyclohexane is high enough, the transportation cost should also increase. Therefore, the second oxidation process raw material must be as low as applicable to prevent any unnecessary flow of money. Last but not least, by using this process the energy use and release are lesser than using other two processes; by phenol and benzene.
The process to break up and forming bonds are easy for cyclohexane than phenol or benzene as cyclohexane doesn’t consist of double bond rather than phenol and benzene which have double bonds of C-C compounds. This advantage will give the plant less energy usage as well as the cost for operating the utilities systems to cool down or heat up the process. 3. PROCESS FLOW DIAGRAM (PFD) 4. PROCESS DETAILS Not all equipments in the process flow diagram (PFD) above will be discussed in this section. Only the most important equipments used to produce adipic acid will be further discussed. 1. First reactor Figure 2. 3: The first reactor Usually, the first oxidation process takes place either in a multiple-stage column reactor or a series of stirred tank reactors with a present of cobalt catalyst. In this process six reactor are needed.
The conditions of the reaction are at 125oC to 165oC and operate at a pressure of 0. 8 Mpa to 2 Mpa. Cyclohexane conversion is limited to only about 10% to 20% in order to increase KA oil selectivity of 80% to 85%. This therefore, will yield 75 to 80 mole % KA oil. The kinetic rate reaction is as below: 2C6H12 + 3/2 O2 C6H11OH + C6H10O + H2O 2. First Splitter Figure 2. 4: The splitter Splitter is use to remove all gasses product from the main stream before undergoes next process. The gasses are removed from the stream and are send to the absorber to be treated before the gas is released to the environment.
Cyclohexane, cyclohexanol and cyclohexanone will then be carried to the cyclohexane column. 3. C6H12 Column Figure 2. 5: The distillation column C6H12 column uses distillation Principe. In distillation column, pure KA oil is being separated from the cyclohexane. The pure KA oil is then send to the second reactor to be further use as reactant for the second oxidation process to be converted to adipic acid. 4. Second Reactor Figure 2. 6: The second reactor In this reactor, oxidation of the cyclohexanol and cyclohexanone mixture with nitric acid with the present of oxygen is taken place. As the reaction is highly exothermic, heat of reaction is usually dissipated by maintaining a high ratio (40:1) of nitric acid to KA mixture.
Nitric acid (55 to 65 percent) and a copper-vanadium catalyst are reacted with the KA mixture in a reactor vessel at 160oC to 260oC and 0. 1 to 0. 4 MPa. Conversion yields of 92% to 96% are attainable when using high-purity KA feedstock. The reaction proceeds as follows: C6H11OH+ C6H10O+ 4HNO3 + 1/2 O2 2 C6H10O4 + 4 NO+ 3 H2O 5. Separator Figure 2. 7: The separator Upon reaction, nitric acid is reduced to nitrogen oxides: NO. The dissolved oxides as well as other gasses are stripped from the reaction product using separator. It then undergoes a treatment process before the gasses are released to the environment. 6. Second Distillation Column Figure 2. 8: The second distillation column
The stream will then undergoes water removal process where all water is withdrawn from the main stream leaving only adipic acid, KA mixture and nitric acid. 7. Third Distillation Column Figure 2. 9: The third distillation column This is the last step of the process in obtaining pure adipic acid. 8. Crystallizer The pure adipic acid obtain from this process is in liquid phase. It then undergoes a crystalline process where adipic acid is then change to solid phase. The solid adipic acid is then packs and ship to be sold local and internationally. CHAPTER 3 MARKET ANALYSIS 1. SUPPLY AND DEMAND Market analysis is one of the method been use to find attractive opportunities in market world and at the same time to avoid any unexpected threats that come from it.
Market analysis can be divided into two forms of purpose which are first, the investors will use the market analysis to survey the potential of the project in the market world before they make any decision either to invest or not. Second, it is the way of marketers to analyze the client’s potential targeted market to improve the strategies of marketing and sales. There are several countries in the world that produce the adipic acid. These countries including the United State of America, China etc. America and China are the most known countries that produce large mass of adipic acid and the oldest countries that leading the manufacturing of adipic acid. The United Stat of America is producing approximately 855 000 tonnes adipic acid per year. On the other hand, China is producing nearly 247 000 tonnes adipic acid per year. Gale Group, 2007) In Asia region, the only performed country in producing this adipic acid is China and others are producing a very little amount for use in domestic. While other countries are just import this adipic acid for use in respective country. The countries that import the adipic acid are Thailand, Singapore and as well as Malaysia. In Thailand, they import the adipic acid is mainly for used in production of nylon. (Gale Group, 2007). Those countries mentioned are the clue of the importance of adipic acid in respective country and also the sign of high potential industrial market if the adipic acid is produce either in those countries.
With the high price of selling value, even though the setup of the plant and also the raw materials prices are expensive, the return rate of the adipic acid is high. This shown that the production of adipic acid is highly return profit. If the adipic acid plant is built in Malaysia, the cost of import adipic acid in Malaysia will decrease as Malaysia is producing our own adipic acid and we will not rely on other country product. Also if Malaysia built the adipic acid plant, such countries as Singapore and Thailand, this will be much better as these countries will import the adipic acid from Malaysia rather that other country to cut the cost of transportation.
Furthermore, Malaysia can export the adipic acid to neighbour countries such as Indonesia and Philippines at the beginning after gaining profit. In Malaysia itself, the demand of adipic acid is more in producing the nylon. For site location matter, the site plant should be near with the source of raw materials such as cyclohexane and nitric acid and also near with the source of demanding industrials or clients. In such manner, the suitable site location is near the source of raw materials is more important rather than the source of demanding customer as to transport a very large mass of raw materials is more expensive than transportation to the customers if the company policies applies.
For that the site location must be near with petroleum based plants as these plants are producing cyclohexane and as well as nitric acid. This shows that the production of adipic acid is highly profitable. 2. ECONOMIC DATA 1. Raw Material Price Estimation The production of the process product is to be expected to reach 100000 tons of adipic acid per annum. Table 3. 1: Cost of raw materials |Reactant |Cost Per Year (RM) | |Cyclohexane |7128000 | |Nitric acid |9377280 | Total cost for raw materials [pic] 2. Equipment Cost Estimation Table 3. 2: Cost of equipment Equipment |Quantity |Cost Per Unit (RM) | |Reactor |7 |222186 | |Distillation Column |2 |528225 | |Separator |1 |26600 | |Stripper |1 |326400 | |Mixer (Inductor) |4 |544786 | |Cooler |1 |18870 | |Heater |1 |44880 | |Component Spillter |4 |528225 | Total cost for all equipment in the process [pic] 3. Operating Labor Cost Estimation Method by Alkahayat and Gerrard [pic] NOL: Number of operator shifts P: Number of processing steps involving particulate solids NNP: Number of non – particulate processing steps Step involving solid: Liquid adipic acid been crystallized using crystallizer to form solid adipic acid. Table 3. 3: Summation of NNP Equipment |Quantity |NNP | |Reactor |7 |7 | |Stripper |1 |1 | |Distillation Column |2 |2 | |Cooler |1 |1 | |Heater |1 |1 | |Mixer |4 |0 | |Component Splitter |4 |4 | |Separator |1 |1 | |Total |17 | [pic] For 1 equipment Number of shifts per year [pic] Number of shifts for an operator per year [pic] Number of operator needed [pic] For all equipment Number of operator needed [pic] Cost of operating labor per year [pic] 4. Land Cost Estimation By considering factory site and also extra site for future build up he estimated land to buy which is 3 acres or approximately 12138 m2. Figure 3. 1: Factory dimension to be built Price per meter square of land [pic] Land cost [pic] 5. Utilities Cost Estimation Based on Table 6. 5 page 264 in Chemical Engineering Design Book. Estimated service requirement: Steam: 2200 kg/hr Cooling water: 5000 kg/hr Electrical power: 10000 kW/d Steam [pic] Cooling water [pic] Electrical power [pic] Total utilities cost [pic] 3. ESTIMATION OF FIXED CAPITAL COST AND WORKING CAPITAL COST From total cost purchasing all equipment is RM 7320546 (E) Table 3. 4: Cost of plant in direct |Description |Percentage (%) Based on E Cost (RM) | |Equipment Installation |39 |2855013 | |Instrumentation (Installed) |43 |3147835 | |Piping (Installed) |31 |2269369 | |Electrical (Installed) |10 |732055 | |Building |15 |1098082 | |Yard Improvement |12 |878466 | |Service Facilities (Installed) |55 |4026300 | |Total of Direct Plant Cost (D) |15007119 | Table 3. 5: Cost of plant in indirect Description |Percentage (%) Based on E |Cost (RM) | |Engineering and Supervision |32 |2342575 | |Construction Expenses |34 |2488986 | |Legal Expenses |4 |292822 | |Contractor’s Fee |19 |1390904 | |Contingency |37 |2708602 | |Total of Indirect Plant Cost (I) |9223888 | Fixed capital cost [pic] Working capital cost can be estimated by 5% of fixed capital cost to cover the cost of initial solvent charge. Working capital cost [pic] Total investment required for project [pic] 4. ESTIMATION OF VARIABLES COSTS AND FIXED COSTS Table 3. 6: Total variable costs Variable Costs Description |Typical Values |Cost (RM) | |Raw Materials |- |16505280 | |Miscellaneous Materials |10% from Raw Materials |1650528 | |Utilities |- |3575313 | |Shipping and Packaging |Usually negligible |- | |Total Variable Costs (VC) |21731121 | Table 3. 7: Total fixed costs Fixed Costs Description |Typical Values |Cost (RM) | |Maintenance |7% from fixed capital cost |1696171 | |Operating Labor |- |2070600 | |Laboratory Costs |21% from operating labor |5088512 | |Supervision |20% from operating labor |4846201 | |Plant Overheads |20% from operating labor |4846201 | |Capital Charges |10% from fixed capital cost |2423101 | |Insurance |1% from fixed capital cost |242310 | |Local Taxes |2% from fixed capital cost |484620 | |Royalties |1% from fixed capital cost |242310 | |Total Fixed Costs (FC) |21940026 | Annual operating cost (TC) [pic] 5. BREAK EVEN ANALYSIS Break even analysis is a way to analyze or to determine the break even quantity for a decision variable. The break even point or QBE is been determine using relations for revenue and cost at different value of variables. Q is linked to fixed costs (FC) and variable costs (VC). The equation been use to calculate the profit is [pic] Where P: Profit in term of RM/year r: minimum sales to break even
VC: variable cost Q: production unit FC: fixed cost To break even, the value of P must equal to 0. [pic] From equation above, the minimum sales to break even is about RM 21733513. 01 per year production. The expected year of return of profit is about 2 – 5 years for optimum production. To calculate the profit return to the company, there are some calculations that have to make as it will show in the next page. 6. DISCOUNTED CASH FLOW Each year the value of money will either increase or decrease depending on the world market. This shows that money has a time value. For calculate pay back time, there are several terms that should been known. pic] [pic] There are two ways to determine the pay back time period which the first one by calculate the NFC until the NFC cumulative reach zero. This method is the simple and easy way to find the pay back time period. On the second method, the usage of NPW formula in calculation until the cumulative of the NPW reach zero. By using the NPW formula the discount rate should been known where the value is retrieve from the actual current market value. Using above calculated data where the capital cost that will be invested for this plant is RM 2. The plant will be expected to been built in 2 years and immediately start after completion of the plant.
The plant will give net profit about 40 millions per year. The discount rate for the market is assume to be 8% where the capital cost be paid in 2 equal installment at the first two years. Figure 3. 8: Calculating net cash flow and net present worth |Year |Earning |Expenditure |NFC |Cumulative NFC |NPW |Cumulative NPW | |1 |0 |12721279 |-12721279 |-12721279 |-11778962. 04 |-11778962. 04 | |2 |0 |12721279 |-12721279 |-25442558 |-10906446. 33 |-22685408. 7 | |3 |10000000 |0 |10000000 |-15442558 |7938322. 41 |-14747085. 96 | |4 |10000000 |0 |10000000 |-5442558 |7350298. 53 |-7396787. 43 | |5 |10000000 |0 |10000000 |4557442 |6805831. 97 |-590955. 46 | |6 |10000000 |0 |10000000 |14557442 |6301696. 27 |5710740. 81 | |7 |10000000 |0 |10000000 |24557442 |5834903. 95 |11545644. 6 | |8 |10000000 |0 |10000000 |34557442 |5402688. 85 |16948333. 61 | |9 |10000000 |0 |10000000 |44557442 |5002489. 67 |21950823. 28 | |10 |10000000 |0 |10000000 |54557442 |4631934. 88 |26582758. 16 | [pic] The entire rate will be in RM currency. For an optimum period of pay back is in range of 2 – 5 years from the production year. In this case, both ways show that the plant will give profit to the company after 3 years production, show that the plant is feasible.
For accurate number of years, the calculation will be done using the interpolation method where the pay back time will be on 5. 09 years starting from the plant building or 3. 09 years after the plant operation. CHAPTER 4 SITE SELECTION AND PLANT LAYOUT 1. INTRODUCTION The location decision is very important. Location greatly affects both fixed and variable costs. Location has a major impact on the overall risk and profit of the company. Traditionally, companies have sought to acquire competitive advantage over their rivals through their choice of location. In a historical context, firms tended to establish their factories for reasons of economic geography.
The example are proximity to raw material source, proximity to relatively cheap and abundant energy, availability of relatively inexpensive manpower or specialist skills and good transport links with materials suppliers and markets. In more recent times the location decision has been influenced by government intervention. The example are high tariff duties imposed on imports which encourage exporters to that country to consider setting up local operations, investment incentives in the form of tax relief and grants and the provision of infrastructure, especially improved transport communication (Mobley, Keith, 2006). In today’s world the decision is more complex.
Markets are more sophisticated, skills can be in short supply, technological change can soon outdate newly installed processes, and there has been a phenomenal revolution in communications, both in terms of the physical movement of goods and people and of information around the world. As a consequence, companies often have to consider a wide number of options, and the eventual decision is based on optimizing the perceived net benefits. The following are the key factors in selecting a location are protected markets and economies of scale, government influences, corporate and people matters. 2. CRITERIA OF SELECTION The objective of selecting the best location for the plant is for maximum operating efficiency and effectiveness by minimizing operating cost and achieving maximum revenues.
A few factors will be considered in selecting the site. It is crucial from several aspects such as to maximize profitability, to reduce negative impact to the environment and also to reduce the number of un-employment in a country. Those factors are tabulated in table 4. 1. Table 4. 1: List of factors in selecting the site |(a) Designation as a heavy industrial development area (‘light’ industry | (b) Availability of utilities- In Malaysia, the availability of| |usually means assembly of electronic components, small metal fabricators, |utilities such as water, power, telecommunication system and sewage | |etc. , and a major chemical plant would not be acceptable). treatment are in the good manner and can easily be obtain to operate | | |the company. | |(c) Prior existence of similar chemical plants and location of other |(d) Existing roads and services, e. g. electricity, gas, water, etc. | |industrial centres. | | |(e) Appropriate terrain, sub-surface, drainage, etc. |(f) Suitable access for transportation of raw materials and chemicals,| | |and for construction of a chemical plant. |(g) Proximity to major transportation networks, e. g. roads, railways, |(h) Availability of a local workforce and distance from local | |airports, waterways, ports that can assist to boost up the selling of |communities. The labor is important in order to provide workforce and | |adipic acid. This is a major consideration in the location of a plant. In |maintain production. The workforce in Malaysia is young, educated and | |some cases direct pipelines for the transportation of chemicals or |productive, proving to be one of the best in the region. | |utilities (e. g. water, gas, and oil) may be the most economical method.
The| | |cost of transportation by tanker (road, rail or sea) is reduced if a return| | |load can also be carried. | | |(i) Availability of domestic water and plant cooling water |(j) Proximity to both the raw materials supply and the market for the | | |product chemical. One possible location is a site near the source of | | |the raw materials. | |(k) Existence of services equipped to deal with a major industrial |(l) Climatic conditions, e. g. umidity, maximum wind velocity and its | |accident. |prominent direction, rainfall, etc. Climate in Malaysia is stable | | |throughout the year and this seldom affects the production of adipic | | |acid | |(m) Proposed or possible government restrictions regarding industrial |(n) Political and strategic considerations – Political consideration | |development or discharge emissions. |is an important aspect in an industry as it helps the growth business | | |by providing incentives and commodity for the industrialist.
The | | |government also shows their support by providing lands for industrial | | |estate which is priced according to state and area | |(o) Price of land. |(p) Local community considerations – The area chosen needs to have a | | |community that is able to provide basic needs for the labors. The | | |basic need includes banks, shop lots and even schools for their | | |younglings. | |(q) Possibility of earthquakes, subsidence, avalanches, etc. |(r) Availability of government regional development grants or tax | | |incentives, subsidies, etc. | 3. POTENTIAL SITES Several sites in Peninsular Malaysia have been taken into consideration.
The site that was considered is Gebeng Industrial Area Kuantan, Pahang Darul Makmur, Tanjung Langsat Johor Bahru, Johor Darul Takzim, and Teluk Kalong, Terengganu. These sites are industrial parks that produce petrochemical and heavy industrial used. Government assistance during the construction phase and possibility also in the form of tariffs is possible depend upon which site will be located. The raw material supply is near and save the transportation cost. 1. Description of Each Selected Location 1. Gebeng Industrial Area Kuantan, Pahang Darul Makmur Gebeng has all the markings as an important petrochemical centre in the country, strategically located closely to integrated upstream oil and gas production centres in Kertih, an indigenous petroleum industry zone in Malaysia.
It has the necessary infrastructures such as logistic advantages in accessing to supplies of reliable and uninterrupted petroleum products and world-scale petrochemical and plants. Figure 4. 3 show the layout of the Gebeng Industrial Area. The facilities exist in this area. I. Transportation Gebeng is accessible to an extensive network of quality roads that connects throughout Peninsula Malaysia. A proposed national highway linking the Eastern Corridor to the Western Peninsula Malaysia would further accelerate the development of Eastern Peninsula Malaysia and more importantly Gebeng. There is a 73 km railway link that connects Kerteh-Kemaman-Kuantan (including Gebeng Kuantan Port). The railway link is capable to haul cargo in large volumes and in bulks making
It is highly economical, safe, reliable and consistent mode of transportation for the movement of raw materials and finished products of petrochemical materials both in liquid and solid state. II. Sea facilities Gebeng benefits enormously from its close proximity to the Kuantan Port where it serves as Peninsular Malaysia’s gateway to the Pacific Rim. This has encouraged business growth within the area. Figure 4. 4 show the port layout of Gebeng Industrial Area. III. Availability of utilities The current electricity supply capacity in Gebeng supplied by Tenaga Nasional Berhad (TNB), Malaysia’s national electricity provider is at 132 kV and 275kV.
Currently water supply in Kuantan is at a capacity of 32 million gallon per day. Extensive work is being carried out by the water work department to double this capacity in a bid to establish constant supply of water to Gebeng. In addition to the existing infrastructure facilities in Gebeng, the Centralised Utilities Faciliites (CUF) (Figure 4. 5) has been implemented by Petronas to supply electricity, industrial gases, steam and demineralised water. The heighten utilities demand is a result in the increased investment in Gebeng whereby creating a multitude opportunities for providers to broaden related activities such as in the supply of oxygen, nitrogen, hydrogen and carbon monoxide. IV. Availability of labor
With increasing demand for skilled workers, training facilities such as Industrial Training Institute of Kuantan (ILP) has located a training centre within Gebeng to facilitate the provision of highly skilled workforce to the requirement of industries. The training schemes of ILP is recognised by the National Vocational Training Council and the courses offered relates to the industries set up within Gebeng such as general machining, welding, metal structural preparations and erection, sheet metal fabrication, electrical wiring, industrial and consumer electronics as well as architectural draughtsmanship. This ensures necessary labour skills are readily available for operations at Gebeng whenever required. V. Storage facilities
Petroliam Nasional Berhad (‘Petronas’) is the national oil company, a having exclusive ownership and control of oil and gas resources is actively operating in the industrial region of Gebeng. Petroliam Nasional Berhad (‘Petronas’) is the national oil company, a having exclusive ownership and control of oil and gas resources is actively operating in the industrial region of Gebeng. VI. Health and Safety In promoting for an incident and disaster-free environment for chemical and petrochemical employees at all levels, the Kuantan Fire Department had established a fire station within the Gebeng Industrial Area. In addition, a volunteer crisis management organisation has been set up under the Gebeng Emergency Mutual Aid (‘GEMA’) offering expertise to counter emergencies in the vicinity of Gebeng and Kuantan Port.
GEMA is a joint effort between government agencies, Kuantan Port and chemical and petrochemical manufacturers located at Gebeng Industrial Area and Kuantan Port Industrial Area such as Amoco, BASF, Kaneka, Eastman Chemical, Malaysian Oxygen, Exxon Oil, MTBE/Polypropylene Malaysia, Polyplastic Asia Pacific, Shell, W. R. Grace Specialty Chemicals, Gas Malaysia and Flexsys Chemicals. VII. Local Authorities The Pahang State Development Corporation (‘PSDC’), a government agency entrusted by the state government to develop Gebeng Industrial Area had established a site office at the Gebeng Commercial Centre which is located within the Gebeng Industrial Area.
The office’s function is to enable delivery of continuing efforts in building Gebeng as a leading chemical and petrochemical centre. It also serves as point of reference to adress investors’ needs arising from day-to-day operations. Another government agency, SIRIM, the accreditation body in Malaysia for certification of manufactured products for their quality in meeting benchmarks and standards will be operating a centre within 5 kilometres from Gebeng Industrial Area. VIII. Effluent disposal facility The ETP Eco-complex is created as a concerted effort to provide an efficient and effective waste management alternative for the handling and disposal of industrial waste and byproducts generated by the different industries in Kuantan and the Eastern Corridor.
The ETP Eco-complex will provide land area and facilities for the handling, storage, warehousing, pre-treatment, disposal and recycling of waste materials generated by the existing chemical and petrochemical industries in the Gebeng Industrial District and surrounding vicinities. Figure 4. 1: Location of Gebeng Industrial Area Source: Pahang State Development Corporation website (2008). Figure 4. 2: Three phases of industrial area in Gebeng Source: Pahang State Development Corporation website (2008). Figure 4. 3: Layout of Gebeng Industrial Area. Source: Pahang State Development Corporation website (2008) Figure 4. 4: Port layout of Gebeng Industrial Area Source: Pahang State Development Corporation website (CUF) Figure 4. : The Centralised Utilities Faciliites (CUF) Source: Pahang State Development Corporation website (2008) 2. Tanjung Langsat Pasir Gudang, Johor Darul Takzim Tanjung Langsat strategically located in the heart of South East Asia – one of the world’s biggest market and fastest growing region. The existing Pasir Gudang Industrial Estate and the strong potential of the new Tanjung Langsat Industrial Estate are the main foundation and catalyst for sustainable growth and future success. Plate 4. 1 is the picture of Tanjung Langsat Industrial complex and figure 4. 6 is the layout of Tanjung Langsat Industrial complex. The facilities exists in these area are list below. I. Availability of Labor
Educated workforce which are talented, young, educated and productive workforce, multilingual workforce speaking two or three languages, including English, comprehensive system of vocational and industrial training including advanced skills training and harmonious industrial relations with minimal trade disputes. II. Sea facilities Tanjung Langsat Port Sdn Bhd With easy access to the rest of the world due to its closeness to the international shipping lane and its connectivity with other modes of transport (Figure 4. 7). III. Availability of Utility The current electricity supply capacity in Tanjung Langsat supplied by Tenaga Nasional Berhad (TNB). Available 24 hours from Tenaga Nasional Berhad with transmission voltages at 257kV, 132kV, and 66kV while distribution voltages at 33kV, 11kV, 6. 6kV and 0. 15kV and three phases or 0. 39kV. Several IPPs will also make their presence here to support the supply. There is also Biofuel Park located in Tanjung Langsat Industrial Complex, where an area of 1,200 acres has been allocated for biofuel project and related industries (Figure 4. 8). Kulim (Malaysia) Berhad has purchased 50 acres of land in Biofuel Park producing 100,000 TPA of biodiesel. Amongst the infrastructure provided in Biofuel Park are the tank farm and pipeline facilities that will be managed by Langsat Bulkers Sdn. Bhd. located at Tanjung Langsat Port area. The pipeline services will connect the factories, the tank farm and the jetty.
Under the Peninsular Gas Utilisation Project, Tanjung Langsat will host further developments in gas utilisation as fuel and feedstock in petrochemical industries, steel plants and chemical industries. [pic] Plate 4. 1: Picture of the Tanjung Langsat Industrial Complex Source: TPM Technopark Sdn. Bhd website (2008) Figure 4. 6: Layout of the Tanjung Langsat Industrial Complex Source: TPM Technopark Sdn. Bhd website (2008) Figure 4. 7: Tanjung Langsat Port Sdn. Bhd Source: TPM Technopark Sdn. Bhd website (2008). Figure 4. 8: Biofuel Park located in Tanjung Langsat Industrial Complex Source: TPM Technopark Sdn. Bhd website (2008). 3.
Teluk Kalung Industrial Park Under the East Coast Economic Region (ECER), Terengganu is expected to become a hub for the oil and gas and petrochemicals industries, a centre of educational excellence as well as an agriculture hub. Also at Teluk Kalung, the industrial area is situated adjacent, and offer excellent access to Kemaman Port. Industrial available are Heavy Industries, Chemicals and Petrochemicals. Terengganu will also be designated as the centre of educational excellence with the establishment of the 283ha Taman Ilmu (Knowledge Park) in Besut, that will be able to accommodate six universities and several industrial training centres.
The designated Kuala Terengganu City Centre (KTCC) will be developed into a high impact urban development to reflect the State capital’s role as a tourism and invest