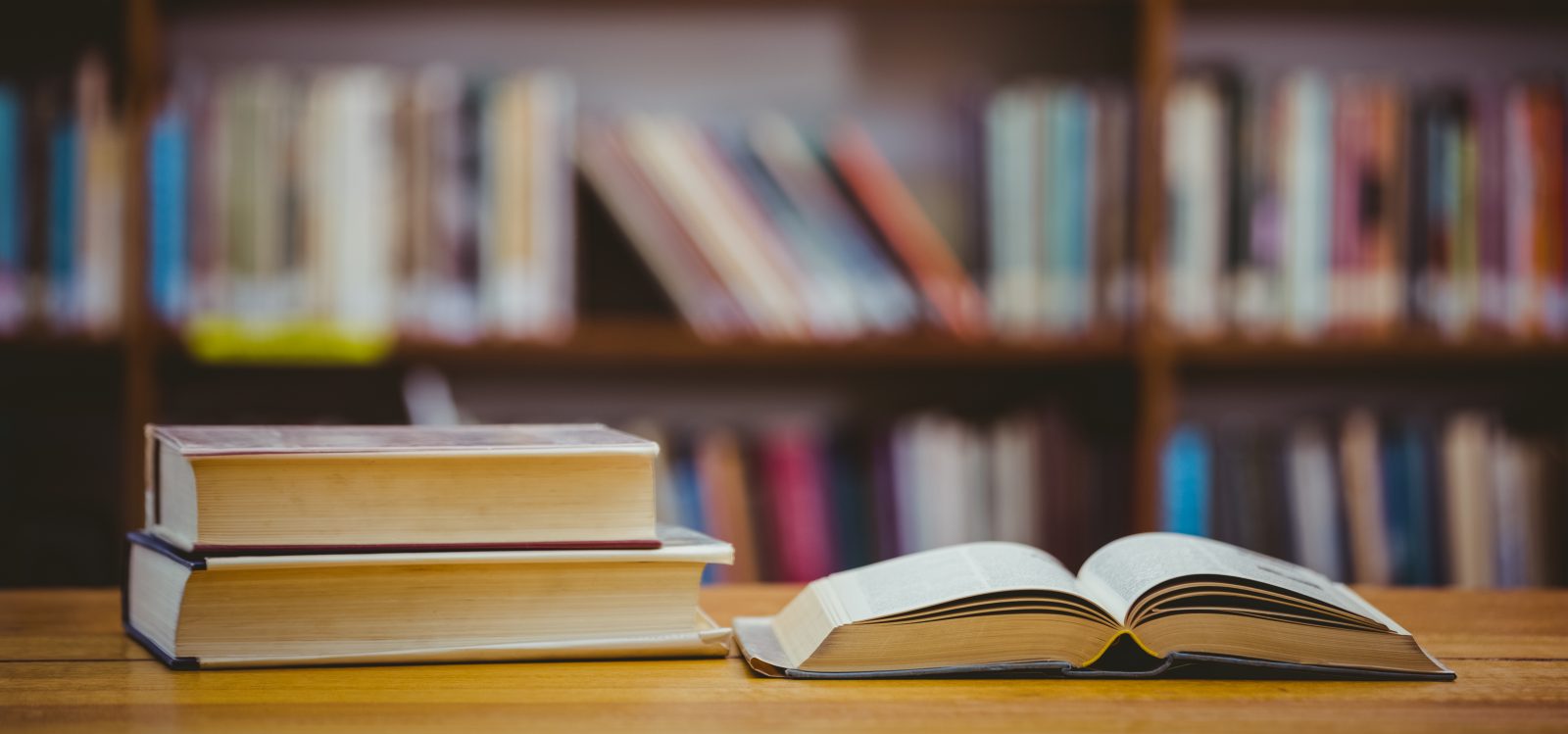
CocaCola’s Operations and Management Processes
Coca-Cola, (Coke) is a soft drink manufactured by Coca Cola limited. The first Coca Cola product arrived in the United Kingdom in 1900 when the Asa Chandler brought five gallons of syrup to London, during a first. The first sale of Coca Cola occurred on the 31st of August 1900.
However, the company did not sell its flagship product regularly until the early 1920s (Coca Cola Journey, 2018). Over the years, the company has established multiple manufacturing plants to produce syrup which it sells to its partners to produce the finished drink. Two companies are responsible for the production of its products in the UK, the Coca Cola Enterprises and Coca Cola Great Britain.
This paper will focus on operations management of Coca Cola enterprises, the firm responsible for manufacturing and distribution of its products. Operation Transformation Processes Coca Cola employs continuous flow manufacturing process to transform raw materials into Coca Cola drink.
The raw materials of the soft drink include water, sugars, flavors, and fruit juice.The first stage is purification of water used in the production of syrup, which aims at removing impurities from the water. Some of the key impurities removed in the process include taste and odor, suspended matter, organic matter, microorganism and alkalinity (HR Elements, 2015). Multiple barrier water treatment systems are generally used.
The second stage of the process is formation of PET bottles. The process involves blow molding of performs, labelling of bottles and rinsing of bottles. Syrup is prepared by dissolving sugar into the treated water and later filtering the water to remove impurities. The process yields a simple syrup, which is later mixed with concentrates and flavors to form the final syrup. Using flash pasteurization, the syrup is treated to remove impurities and extend its shelf life (HR Elements, 2015).
The final syrup is mixed with cooled treated water to form, and then carbonated to form the final product. Filling and packaging process is continuous, with containers filled, hermetically sealed, labelled coded and tested. Glass bottles are placed in boxes, with canned and non-returnable plastic bottles packed into multi-packs. The packaging and the bottles or cans are combined through a rapid filling process.
Each bottle or can is inspected for leaks, gaps and deformities before it is packaged and sent to warehouses (HR Elements, 2015). The drink is distributed to wholesalers, who then distribute it to retailers, where it is purchased by consumers.
Trade-Off Analysis
Syrup production and soft drink production require complex systems. They involve transfer of energy, materials and information between tasks. Cost of coordinating these tasks tend to impede the ability of an organization to exploit synergistic benefits of diversifying into related products, including new varieties and tend to cause problems to the organization design (Zhou & Wan, 2017).
The company relies on its franchisees to produce the finished product, with the company providing the syrup and overseeing the production process. Use of franchisees to produce the product in different locations improves the flexibility of the production process, and reduces the potential for delays, as a bottler can produce the product in a specific location and supply the product to that specific geographical location (Kench, et al., 2012).
In terms of price, the production of Coca-Cola is capital intensive. In addition, production lines are specialized which increases switching costs, ensuring that the production process is only efficient when only one variety is produced at a given production line. The cost of operations and building of factories is low.
There are several reasons. First, the company only produces syrup, with franchisees being responsible for financing their blending and bottling plants. Second, majority of its lines are focused in the production of a single product –syrup. This means that its manufacturing plants benefit from economies of scale. Third, the production lines are specialized to produce a single product, which improves their efficiency.
Although franchising reduces decentralizes control, the company has implemented a robust quality control system to ensure that all its products meet the required standards. Coca-Cola employs both Quality Assurance and Quality Control to monitor production (HR Elements, 2015).
Quality control focuses on the manufacturing processes, while quality assurance focuses on the entire operations of the company, including the operations of its franchisees and the quality of products supplied to the company.
Through quality control and assurance, the company is able to control the dependability of its product systems and the quality of its products. In the production of syrup and bottling of final products, Coca Cola employs continuous manufacturing to enhance speed of production (HR Elements, 2015).
Continuous manufacturing is a manufacturing process where the raw materials or inputs are continuously processed and treated. Unlike traditional batch production, the production process can continue perpetually. In continuous manufacturing all production steps are carried within a single facility. As such, there are few interruptions and delays related to the transfer of production material to other facilities.
The process allows for high production speeds while optimizing quality control and improving efficiency. In addition, continuous manufacturing processes allow for automated quality control without interruption. Continuous manufacturing has been found to reduce cost of operation, capital expenditure, and better quality control and reduction in transport costs (Lee, et al., 2015).
Operation Improvement Techniques
The Coca Cola Company employs continuous manufacturing, just-in time strategies and made to stock method to improve operation processes. Continuous manufacturing, as discussed earlier, involves continuous processing of materials to produce goods.
The products are made in a continuous manner, and the production system tends to be highly standardized and automated. Continuous manufacturing is enabled by hole-in-the-wall operations. For example, production facilities of canned Soda will be built near a production facility of cans, allowing for the integration of the two manufacturing processes.
On the other hand, bottling companies will be located adjacent to a water purifying facility to reduce wastage and transport costs (HR Elements, 2015). Given the complexity of the company’s supply chain, franchises are encouraged to ensure that all raw materials for the production process arrive ‘just-in-time’ to ensure that they are processed into the final product to meet demand. Coca-Cola works closely with its franchisees to ensure that all production materials are present during production.
In addition, Coca-Cola enters into distribution partnerships to ensure that the products are transferred to consumers without any delays. The advantage of just-in-time concept is that it reduces waiting time, and thus minimizing cost of storing inventory and production time (Xu & Chen, 2016).
The made-to-stock (MBS) method is used for this process. Stock produced by the company is in bulk. All stocks are then distributed to the wholesalers and retailers. MBS is more advantageous than made to order, as MBS does not influence the production batches, allowing for continuous production of products to fulfill the current demands (Rajagopalan, 2002; Kober & Heinecke, 2012).
Coca Cola also employs co-ordination to ensure there are sufficient amount of product to meet demands (HR Elements, 2015). For example, if a company is undergoing renovation, another is allowed to increase production to meet fill the gap. Challenges and Potential Improvements While the production processes are highly efficient, Coca Cola faces multiple challenges outside its production facilities.
Generally, the company employs Just-In-Time inventory management, where a facility only holds raw materials needed for four to five days of production. The approach leaves little room for mistakes during supply chain management, production and forecasting. Coca Cola should ensure that it has sufficient means of forecasting changes in supply of products and changes in demand. In addition, this means that the company has to enter into long term contracts with suppliers and contractors.
The company also faces challenges related to water acquisition. Water is the main raw material for its products. As demand for water increases, water resources will become scarcer and more expensive, which may reduce the profitability of its operations. The company needs to invest in treatment plants for water recycling and treating of waste or gray water.Production in Coca Cola production facilities is highly automated.
It is thus vital for the company to invest in a high skilled workforce to manage its production lines. Disruption in production can cause delays in meeting consumer demand, which in turn may affect customer satisfaction. Furthermore, continuous production tends to stress machines, resulting in high risk of failure.
The key disadvantage of continuous production is that it is associated with high cost of switching product, if there are changes in demand for a specific product. The company should strive to develop specific lines for specific products, without switching production lines to reduce the costs associated with switching.