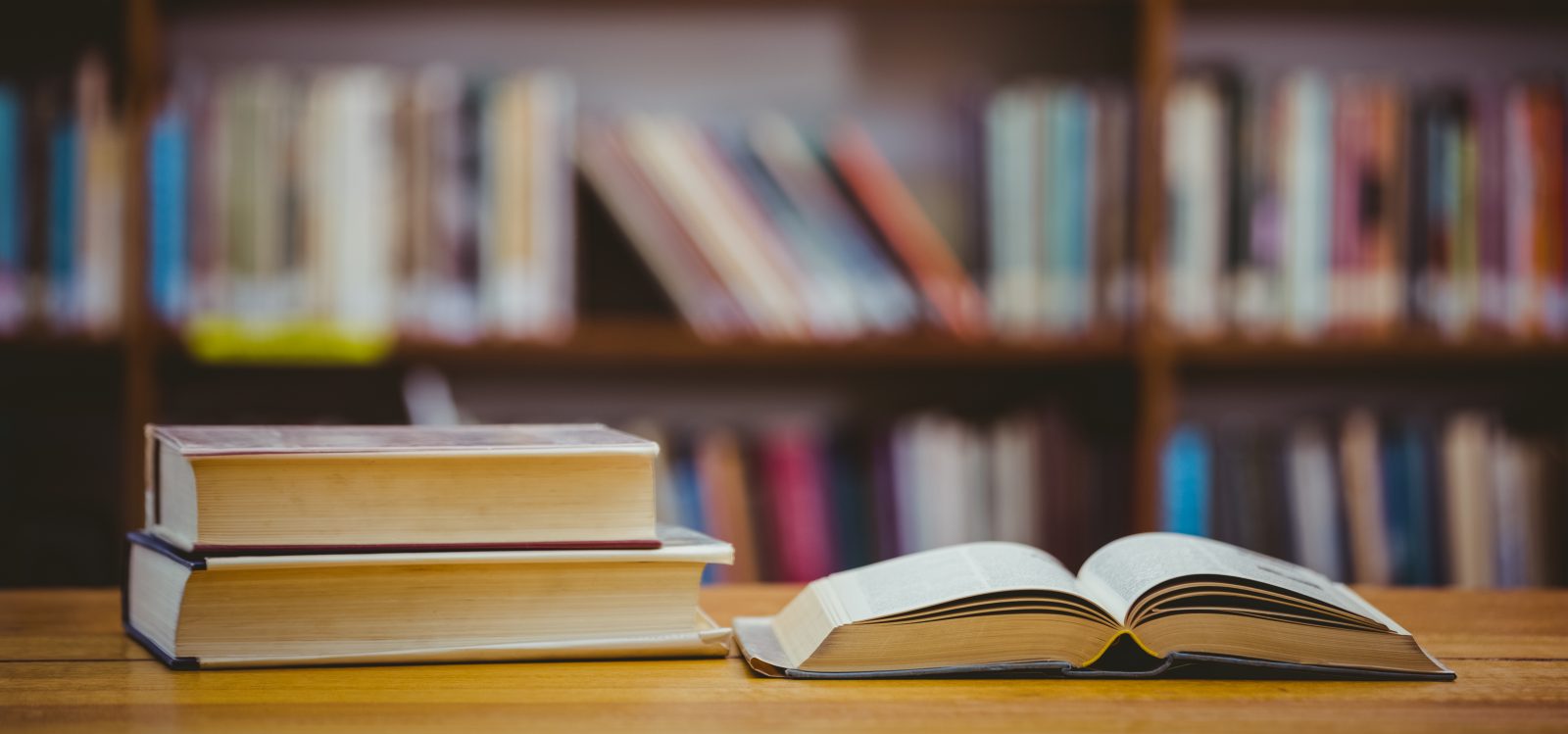
Mig Welding
What is MIG Welding? Metal Inert Gas (MIG) welding, also sometimes called Gas Metal Arc Welding (GMAW) is a process that was developed in the 1940s for welding aluminum and other non-ferrous metals. MIG welding is an automatic or semi-automatic process in which a wire connected to a source of direct current acts as an electrode to join two pieces of metal as it is continuously passed through a welding gun. A flow of an inert gas, originally argon, is also passed through the welding gun at the same time as the wire electrode. This inert gas acts as a shield, keeping airborne contaminants away from the weld zone.
Advantages and Disadvantages of MIG Welding The primary advantage of MIG welding is that it allows metal to be welded much more quickly than traditional “stick welding” techniques. This makes it ideal for welding softer metals such as aluminum. When this method was first developed, the cost of the inert gas made the process too expensive for welding steel. Over the years, the process has evolved, however, and semi-inert gases such as carbon dioxide can now be used to provide the shielding function, which now makes MIG welding cost-effective for welding steel.
Besides providing the capability to weld non-ferrous metals, MIG welding has other advantages: ? It produces long, continuous welds much faster than traditional welding methods. ?Since the shielding gas protects the welding arc, this type of welding produces a clean weld with very little splatter. ?It can be used with a wide variety of metals and alloys. The primary disadvantages of MIG welding include the following: ? The equipment is quite complex, as MIG welding requires a source of direct current, a constant source and flow of gas, as well as the continuously moving wire electrode.
Plus, electrodes are available in a wide range of sizes and are made from a number of metal types to match the welding application. ?The actual technique used is different from traditional welding practices, so there is learning curve associated with MIG welding, even for experienced welders. For example, MIG welders need to push the welding puddle away from them and along the seam. ?The necessity for the inert gas shield means that MIG welding cannot be used in an open area where the wind would blow away the gas shield.
Since its development in the middle of the 20th century, MIG welding has become commonplace in many manufacturing operations. For example, it is commonly used in the automobile industry because of its ability to produce clean welds, and the fact that it welds metals quickly. What is TIG Welding? Tungsten inert gas (TIG) welding is the process of blending together reactive metals such as magnesium and aluminum. The TIG welding method became popular and useful in the early 1940s and, as a result, has greatly propelled the use of aluminum for welding and structural processes.
TIG welding is commonly used for both high quality and manual welding. During the process of TIG welding, an arc is formed between a pointed tungsten electrode and the area to be welded. As a result of the gas shield, a clean weld is formed. This prevents oxidization from occurring. The type of gas shielding typically used for TIG welding is argon, helium, or a combination of both. When combined, these two gases can ensure a higher welding speed and welding penetration. Argon is the preference of most welders when it comes to TIG welding.
It is often used simply because it is heavier than air and provides better coverage when welding. With TIG welding, one can perform a variety of weld types on several different metals. Steel and aluminum, however, are the two most widely used metals. The filler rod is another important aspect of TIG welding. Usually made from the same material as the base metal, it is used for reinforcing joints and welding heavy metals. There are several different types of joints designed for use with TIG welding.
These include the butt joint, lap joint, corner joint and t-joint. The butt joint can be welded without the assistance of a filler rod. With this type of joint, two pieces of metal are joined together along the seams. With a lap joint, the top edge is welded to the bottom piece in an area between the two overlapping metals. A corner joint involves welding one piece of metal at a right angle to the edge of a second piece of metal in order to form a corner. To create a t-joint, a filler rod is necessary.
The t-joint is created by placing one piece of metal perpendicular to another piece of metal to form a T shape. This type of TIG welding is done along either side of the perpendicular seam. Advantages and Disadvantages of TIG Welding Advantages 1. No flux is used, hence there is no danger of flux entrapment when welding refrigerator and air conditioner components. 2. Because of clear visibility of the arc and the job, the operator can exercise a better control on the welding process. 3. This process can weld in all positions and produces smooth and sound welds with less spatter. . TIG welding is very much suitable for high quality welding of thin materials (as thin as 0. 125 mm) 5. It is a very good process for welding nonferrous metals (aluminum etc. ) and stainless steel. Disadvantages •Setup – TIG welding requires more setup time and is not as user-friendly. •Price – These welds tend to be more expensive and take longer than MIG welding, especially in thicker metals. •Complexity – TIG welding is more complex and requires more skill than the MIG welding process.