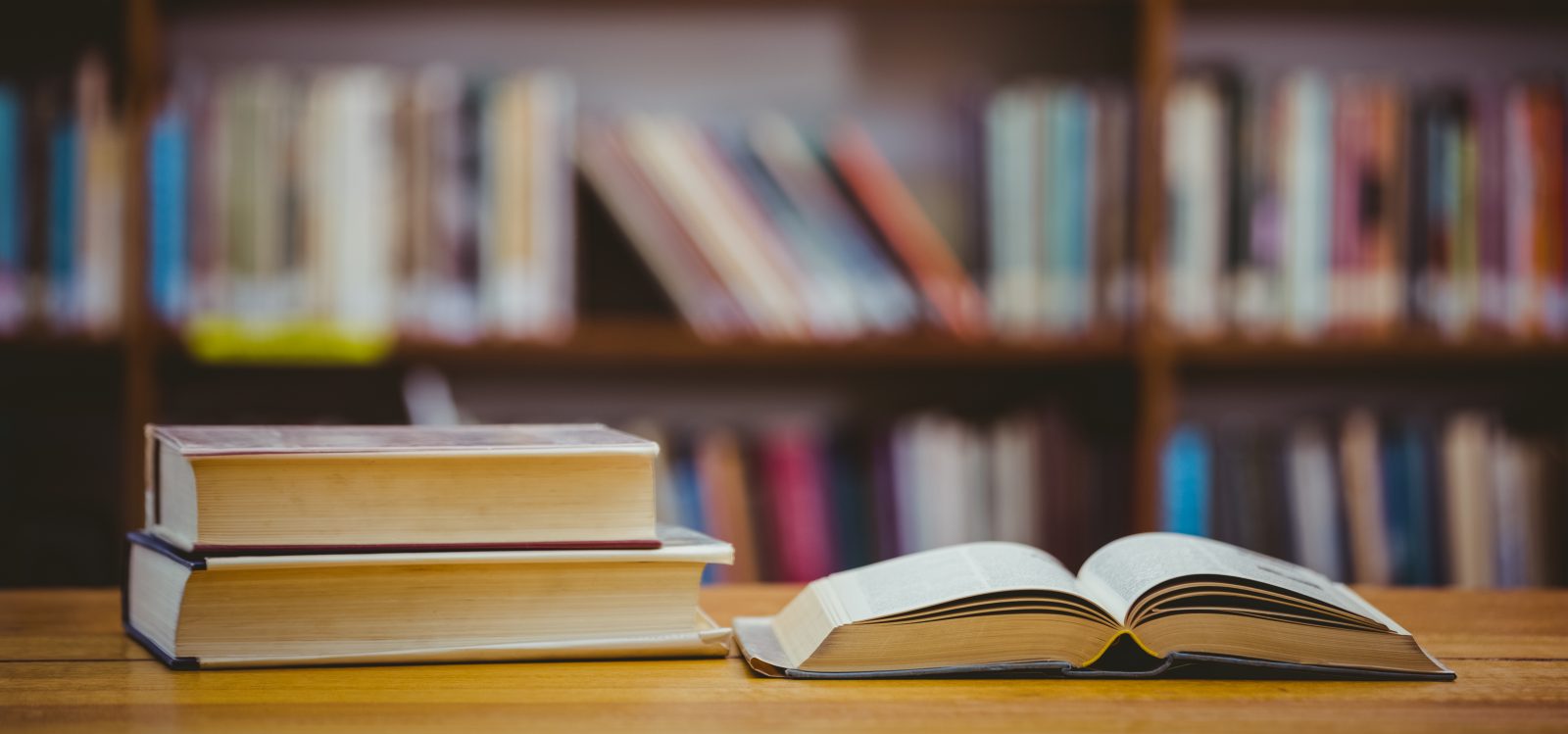
CASE 15 Steinway & Sons: Craftwork, Tradition, and Time Build Grand Pianos Steinway & Sons remains one of the best-known producers of concert pianos in the world. Throughout its great history, the company has shown a distinctive talent at innovation, as evidenced by its more than 100 patents, and is known for quality workmanship. In an age of mass production, Steinway continues to manufacture a limited number of handmade pianos in a unique testament to individual craftsmanship. However, some rival piano makers, such as Yamaha, have tried to challenge Steinway’s dominance of the concert piano market. 1) Can Steinway continue its cherished ways, or will it need to adjust to new circumstances? A Long and Golden History German immigrant Henry Enghelhart Steinway founded Steinway & Sons in 1853. Henry was a master cabinet maker who built his first piano in the kitchen of his home in Seesen, Germany. Henry had built 482 pianos by the time he established Steinway & Sons. The first piano produced by the company, number 483, was sold to a New York family for $500. It is now displayed at New York City’s Metropolitan Museum of Art.
Steinway’s unique quality became obvious early in the history of the firm as proven by its winning gold medals in several American and European exhibitions in 1855. The company gained international recognition in 1867 at the Paris Exhibition when it was awarded the prestigious “Grand Gold Medal of Honor” for excellence in manufacturing and engineering. (2) Henry Steinway developed his pianos with emerging technical and scientific research, including the acoustical theories of the renowned physicist Herman von Helmhotz.
Steinway was owned in the 1970s by CBS, and many concert artists complained that the quality of the pianos had suffered as a result of that ownership. Pianists talked of the “Teflon controversy,” when Steinway replaced some fabric innards with Teflon (it now coats the Teflon with fabric). Steinway was sold by CBS in 1985, and many experts voiced the opinion that Steinway’s legendary quality was returning. Larry Fine, a piano expert, argued that: “a Steinway has a kind of sustained, singing tone that a Yamaha doesn’t have. Yamaha has a more brittle tone in the treble that some jazz pianists prefer. ” (3)
The Steinway Factory Today, the making of a Steinway piano follows the Steinway Tradition. Every grand piano takes over a year to complete and incorporates over 1,000 details that set a Steinway apart from its competitors. A tour of the Steinway factory is a trip back through time, as many of the manufacturing techniques have not changed since 1853. The key steps in the process of crafting a Steinway piano are described below. (4) Using a method that was patented in 1878, the piano manufacturing process begins with the creation of the inner and outer piano rims that give a grand piano its distinctive shape ? his is known as the piano case. Eighteen layers of hard-rock maple, each 22 feet in length, are laminated together and then formed into shape on a giant piano-shaped vise. The rim-bending team centers the wood on the vise and forces it into place with the aid of wood clamps. Meanwhile the soundboard is formed by hand, being “expertly tapered by a craftsman to be slightly thinner at the edges so that it can vibrate properly once it is glued to the piano’s inner rim. ” The bridge of the soundboard must be notched for the piano strings before the soundboard can be placed into the piano case.
A highly skilled craftsman, with years of training, performs this operation because precision is so essential to the quality of the piano’s sound. The veneer for a piano is cut from a single tree to ensure a uniform appearance of the wood finish. It is cut to size and matched for grain, to be applied subsequently to the designated piano. A wooden brace assembly is then crafted to fit within the piano case and to help support the 340 pound cast iron plate that provides the rigid and stable foundation for approximately 40,000 pounds of tension from the piano strings.
This brace assembly is secured to the rim of the piano with fine carpentry joinery and maple dowels. The cast iron plate is then fitted to the piano case and any needed adjustments are made before final installation of the plate. After the soundboard and cast iron plate are properly fitted in the piano case, the piano wires are installed, using both a machine guided stringer and appropriate hand tools. Next, the felt hammers are formed into the proper shape, using glue and a copper forming tool.
The felt hammers are then put on the hammershanks and dampers are installed to prevent unintentional vibration of the piano strings. A master technician painstakingly matches the damper felts to the strings; reaching underneath the piano while looking in mirrors, the master technician adjusts the levers that control each of the dampers. Next, the key board is calibrated by inserting lead weights into the body of each key so that the pressure required to push a key down is the same for every key. Subsequently, a master voicer will adjust the tone quality of each key.
This is done by sticking the hammer’s felt with a small row of needles to reduce stiffness of the felt, resulting in a mellower tone, or by applying a small amount of lacquer to the felt to achieve the opposite effect. Finally, a tone regulator adjusts string tension by turning the tuning pins. Steinway’s process of making a grand piano is complex, requiring numerous processes and procedures that must be performed by highly skilled crafts people. True crafts people produce the world’s finest quality concert pianos. However, not everyone wants or can afford a Steinway piano.
What has Steinway & Sons done to reach other markets while maintaining the Steinway reputation for product quality? Expansion Beyond the Classic Steinway Pianos In recent years, Steinway developed Boston Piano in an attempt to broaden its market. Steinway & Sons designed Boston pianos using the latest computer technology and then outsourced the manufacturing to Kawai, the second-largest Japanese piano maker. By transferring its quality and knowledge of building pianos to the Boston Piano operation, Steinway was able to open up a whole new market.
The Boston Piano venture demonstrated that Steinway’s core competence of hand craftsmanship could be applied in a newer, high-technology manner to a lower-priced market niche. (5) In early 2001, Steinway & Sons introduced a third line of pianos, called the Essex, to complement its Steinway and Boston lines. The Essex line offers two grand and two upright models ranging in price from $5,200 to $17,800. With the Essex, Steinway now provides pianos for every level of musical ability and budget. (6) The question remains, can Steinway continue to operate in the way that has proved successful over the past 150 years?
At the moment, the answer appears to be ? YES. Review Questions 1. The equation specifying that Performance = Ability x Support x Effort is known as the individual performance equation. Using this equation, explain the exceptional performance that is required of and exhibited by the crafts people at Steinway. 2. Use the core job characteristics model to explain the implications of Steinway’s piano manufacturing process for work motivation and behavior. 3. How does Steinway’s piano manufacturing process exhibit the need for teamwork? How does this relate to job enrichment? You Do the Research 1.
How does Steinway continue its emphasis on craftsmanship in this age of mass production? 2. Can any of Steinway’s processes be transferred to other companies? 3. What other consumer products appear to be using a Steinway approach to producing its products? Case Endnotes 1. Cox, M. “Steinway Faces Yamaha Push in Piano Market,” Wall Street Journal, January 19, 1988. 2. Steinway & Sons homepage, http://www. steinway. com. 3. Cox, op. cit. 4. “Factory Tour,” http://www. steinway. com/factory/tour/shtml. 5. Steinway & Sons homepage, op. cit. 6. “Steinway Unveils Essex Piano,” Business Wire, January 23, 2001.