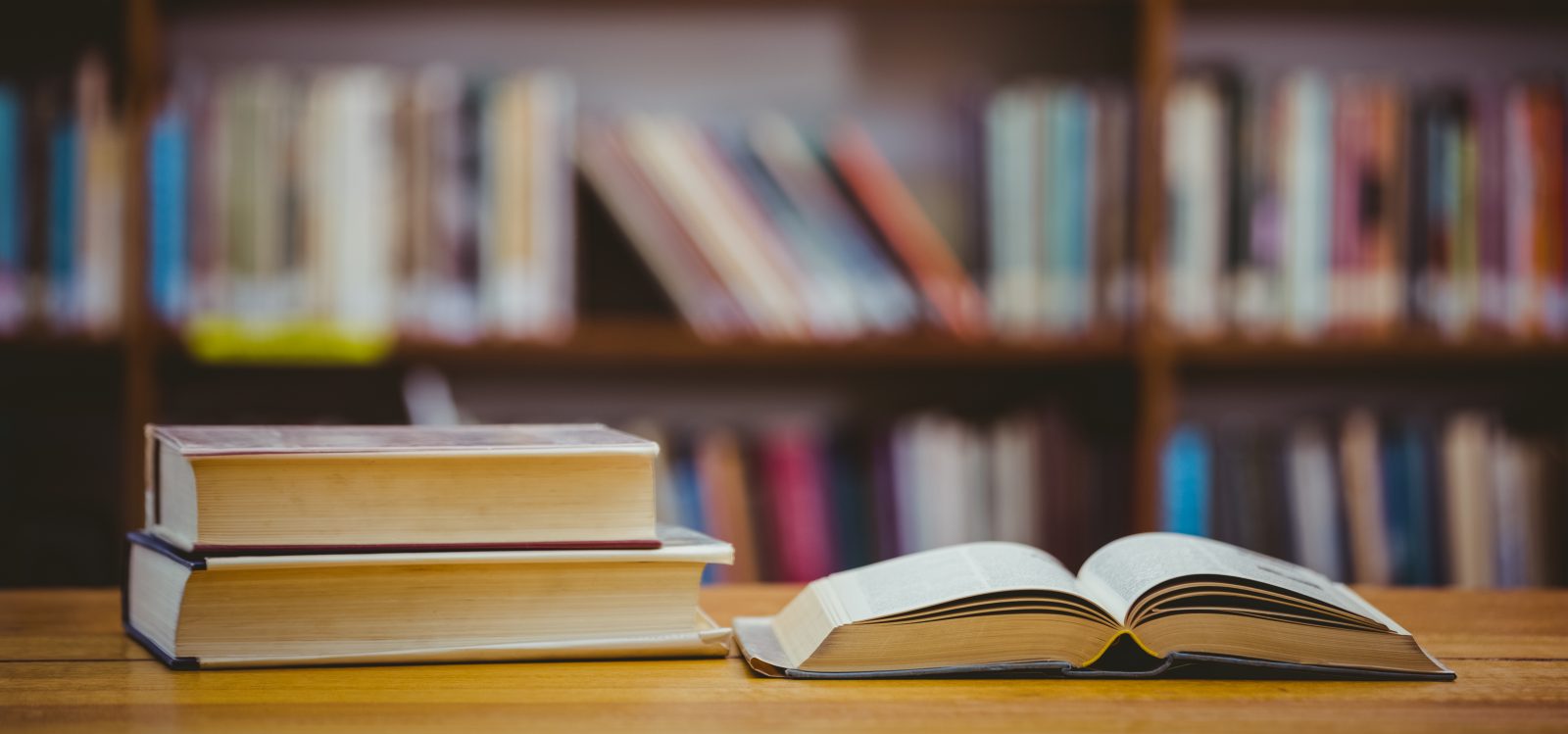
A & D Table of Contents Content | |Page | |Executive Summery | |3 | |Situation Analysis | |3 | |Problems Found in Situation Analysis | |4 | |Strategic Alternatives for Solving Problems | |7 | |Selection of Strategic Alternative & Implementation Plan | |8 | |Appendices | |9 | Executive Summary: A&D has decided that, to remain competitive, they must create an online shopping site that allows their customers to order their products over the internet. Their decision to have the site up and running in time for the Christmas shopping season has only given them 150 days, including the weekends, to achieve the task, which has been calculated out at 555 days based on the tasks involved.
Due to the severe price restrictions that will be realized if they attempt to complete the site using extra assets and overtime, the Build decision is the wrong one for the short term. Since the Buy option does not fulfill their overall needs, and the Build option will take too long, A&D should pursue a Buy and Build plan, with the Buy being the option that best fits their needs in the short term until they are able to Build their own custom site. Situation Analysis: • Sells computer products, accessories, and services to consumers and businesses • Started by Ted Walter in Nebraska in 1988 • In 2000, they had revenues approaching $400 Million • Sales are primarily through their retail outlets and over the phone • Orders handled by call center Before 1999, sales orders written on paper and passed to order-entry clerks o Added time to order, delayed shipment o Poor accuracy- 30% orders required customer callbacks as compared to 5% at competitor • Implemented ERP in 1999 using software from JD Edwards o Could be customized to handle different parts used for production o Customer callbacks reduced to < 1% of the orders o Concerns about maintenance as outside consultants were employed to design and build the system • In 2001, A&D further invested to improve its systems in handling supply chain, payment process, CRM and order management o Reduced costs Significant ROI on its supply chain and warehousing projects • Faced with tough competition and decreasing margins, company decided to explore new segments for growth • Products approaching commodity status – product cost largely the determining factor • Project to create online store • Chris Johnson, Technology Project manager, tasked with creating the online store. • Store had to be up and running before the Christmas shopping season. o Timeline therefore set from early May to October, giving only 5 months Various problems faced A&D in their initial decision as to how the online store should be set up. Build vs. Buy – There were some options where the company could purchase an online store utility rather than build one form the ground up themselves. The decision as to which was better included various factors that led to their final decsion. Pro Buy: The purchased version was cheaper in the intial stages due to there being no need to spend the money on development and programming. • The purchased version would have most of the required functionality already developed. • New versions created by the developer could be purchased without the need to develop in house. Con Buy: • Expensive to buy. • Some functions would be purchased as part of the package that would not be needed. • Need for cusomtization would require hiring programmers. • Maintenance would be more difficult. Pro Build: • System designed for the specific needs of the company • Unique online store could be used to differentiate the company from the competitors. No additional functions that were not needed. • In house tech support knowing the product. Con Build: • Cost of hiring the developers • Available budget for long term support • Time to develop system, test it, and have it up and running. Problems Found in Situation Analysis: Once Webb had decided that building a custom system was the correct path to take, he created a team tasked with designing the averall system. It took them 4 weeks to provide a list of the project planning components that would be needed. These were: • Business requirements • Process Flows • Technical Architecture Requirements • Physical Infrastructure • Prototype • Project WBS • Task Estimates • Project Resources Project Scheduling They then fleshed out the components, and included pricing, asset requirements, and expected time (in days) needed to complete each portion. See Appendix 2 – Project Details. Essential elements of solution: • Must fit within budget • Must be fully integrated for all departments • Must not interupt current state sales • Must be in place for holiday season, at most, 180 days from start of project. • Must be customizeable Problem 1: Assets are over utilized. Based on the WBS, task durations, and assigned assets, it can be seen that some of the assets are over utilized, or have some scheduled tasks that conflict (see following table).
Before an accurate timeline can be created, it will be necessary to level the asset allocations. |1. 3. 1. 1 | Capture Customer Profile |Ryan Neff | |1. 3. 1. 2 | View and Search Product Catalog |Ryan Neff | |1. 3. 1. 4 | Taking Payments |Stacy Lyle | |1. 3. 2 | Create Data Requirements |Stacy Lyle | |1. 4. | Design Capture Customer Profile Pages & Components |Marc Sanders,Ryan Neff[50%] | |1. 4. 4 | Design Taking Payments Pages & Components |Marc Sanders,Stacy Lyle | |1. 4. 5 | Design Submit Order Pages & Components |Marc Sanders,Ryan Neff | |1. 4. 6 | Design Check Order History & Order Status Pages & Components |Marc Sanders,Ryan Neff | |1. 4. 7 | Design Logical & Physical Data Model |Sanjay Vohra,Stacy Lyle | |1. 7. | Build Capture Customer Profile Pages & Components |Developer 2 | |1. 7. 4 | Build Taking Payments Pages & Components |Developer 2 | |1. 7. 6 | Build Check Order History & Order Status Pages & Components |Marc Sanders | |1. 7. 9 | Support Development & Assembly Test |Ryan Neff,Stacy Lyle | |1. 8. 1. 1 | Perform Phase 1 Testing |Marc Sanders | |1. 8. | Perform System Testing |Developer 1,Developer 2,Developer 3,Kara Siposki,Marc Sanders,Ryan| | | |Neff,Stacy Lyle,Todd Eliason | Problem 2: Budget – there is no actual budget available for the project, at least as far as is provided in the case. This means that it is not easy to compare the costs required to build or buy. Based on the scheduling and pricing of the assets in the build scenario, the total cost, including purchasing of the hardware, of the Build option is $ 3,846,781. 92.
Problem 3: The total length of time required to implement the Build option, even after levelling, is 555 days. This will place the completion date into the second year after start of the project. If the project were to start in May of 2003, it would be completed around November of 2005. Problem 4: The bare minimum the project can be reduced to is 127 days Chris Johnson is available. This will meet the goal of under the 5 months, but with his reliance upon the other members fo the team to complete his tasks, this is unlikely to occur. Strategic alternatives for solving problems: To solve the issues being faced, A&D has the following options: 1. Assign more assets to the problem. If the contractors are doubled, or ripled, the testing and implementation stage could be reduced drastically. In particular, the testing stage could be cut down from 286 days to as little as 50 days given sufficient additional assets. For this option to be viable, a thorough evaluation of the costs that will be incurred will be needed. This will then have to be compared against the project budget and a decision made as to viability. 2. Approve overtime. Looking at the critical path (see Appendix 3), it can be seen that there are large periods of testing and implementation that could be shortened if the current assets are require to work overtime. Example: Have the 3 developers work an extra 20 hours a week each for the 160 day System Test.
This will add an additional 1260 hours onto the time spent testing the system. The overall hours of this phase of the project are 10,240, so this extra time will reduce the task duration by a little over 11%, reducing the days to complete the task down to 142. 5 days. There are a number of issues that make this option difficult, and perhaps not worth doing. 1. The 1260 hours are at a higher rate, which will add an additional $306,600. 2. Overtime that lasts for more than 2 weeks begins to cause issues with work quality, which will result in additional oversite, increasing the hours having to be worked by someone else. This will negate some of the extra hours benefit, and will increase the costs. 3.
Since there are an additional 5 people tasked with the testing, it may not be possible to have them work additional hours since they may be required to work on other areas fo the project. Increasing their time to include overtime will reduce the individual task times, but the balance between time savings, cost increase, and quality impact may make this option too expensive. 3. Move away from the Build option and purchase a suitable commercial product that meets the minimum project goal. Even in 2003, the price of purchasing online shopping software was still fairly low. For example, Shopfactory Gold, a current Shopping Cart package, only costs $999.
The additional costs associated with customizing the software Selection of Strategic Alternative and Implementation Plan: The cost of buying and setting up an interim Shopping Cart program is small enough that this should be the initial action to take. Something has to be available and working before the Christmas shopping season, and this will at least meet the needs to a point. Short term, A&D should therefore make the decision to Buy instead of Build, with a long term plan of developing their own online store. By doing this, they will also be able to pinpoint the parts of the store that work well, and incorporate similar functionality in their own Build.
They will also be able to take a little more time in development, reducing the chance of increased errors and customer complaints. Appendices 1: Cost of Project | |Pre-Leveling |Post-Leveling | |Total Days to complete Project |545. 5 |555 | |Total cost for labor |$ 3,746,482. 01 |$ 3,748,281. 92 | |Total cost for Physical Infrastructure |$ 98,500. 00 |$ 98,500. 00 | |Total cost for Project |$ 3,844,981. 01 |$ 3,846,781. 92 | 2: Project Details WBS |Name |Duration | | | |(days) | |1 |Overall Project |555 | |1. 1. 1 | Manage Project |127 | |1. 2. 1 | Gather Business Requirements |8 | |1. 2. 2 | Design Business Process Flows |4 | |1. 2. 4 | Create Operational Requirements |15 | |1. 3. 1. | View and Search Product Catalog |6 | |1. 3. 1. 3 | Updating and Calculating Shopping Cart |3 | |1. 3. 1. 5 | Submit Order |4 | |1. 3. 1. 6 | Check Order History & Order Status |3 | |1. 4. 2 | Design View and Search Product Catalog Pages & Components |13. 5 | |1. 4. | Design Updating and Calculating Shopping Cart |6 | |1. 4. 4 | Design Taking Payments Pages & Components |12 | |1. 4. 8 | Design ERP Interface |24. 5 | |1. 5. 2 | Create System Test Plan & Test Cases |20 | |1. 5. 3 | Write System Test Scripts |22 | |1. 8. | Perform System Testing |160 | |1. 8. 3 | Perform Validation Testing |80 | |1. 9. 1 | Implement System |80 | |1. 9. 2 | Deploy To Production |8 | |1. 9. 3 | Project Wrap-up |94 | [pic] [pic]