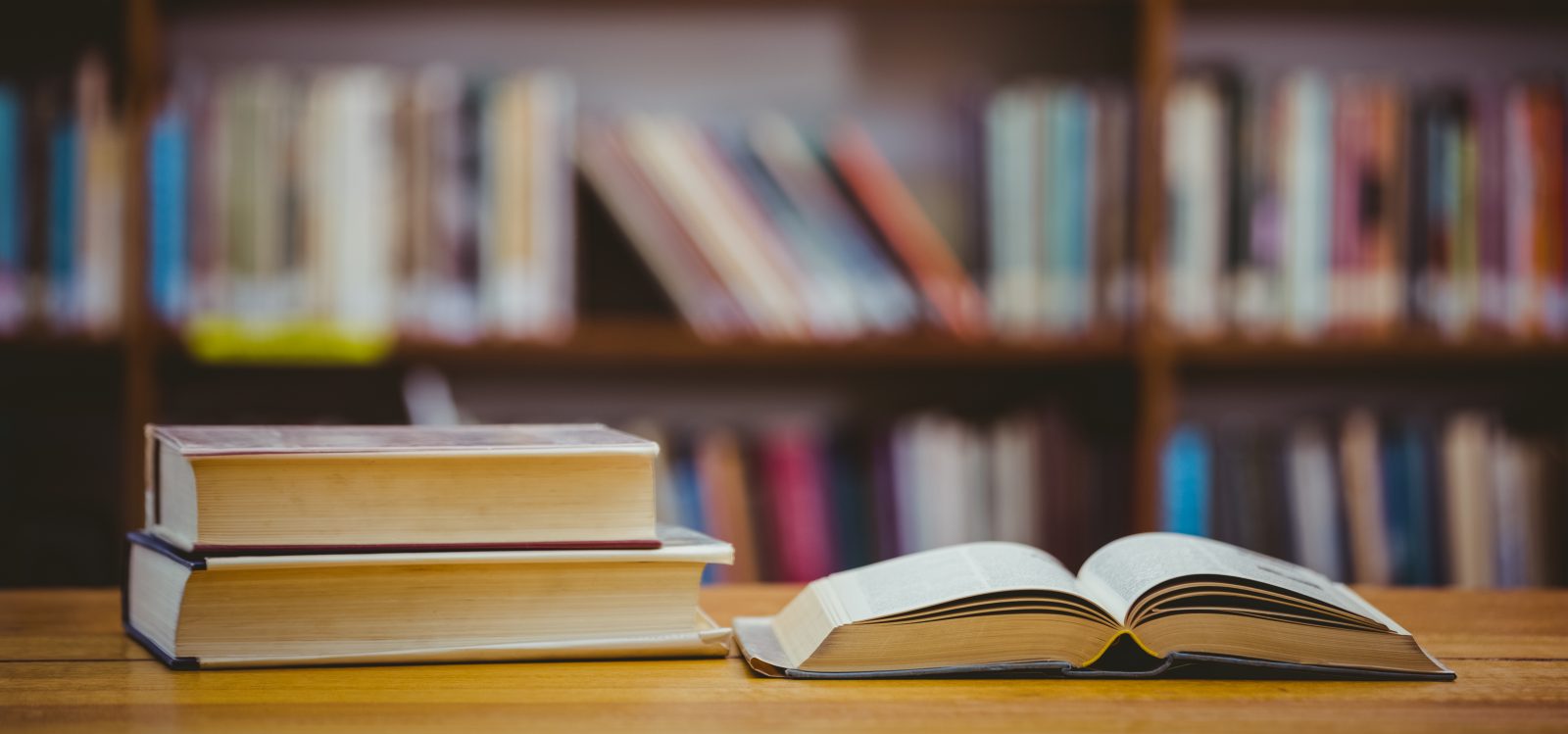
CHAPTER 1 INTRODUCTION The seismic force-resisting system of a building structure is composed of vertical elements, horizontal elements, and the foundation (Fig. 1. 1). The vertical elements extend between the foundation and the elevated levels, providing a continuous load path to transmit gravity and seismic forces from the upper levels to the foundation. The horizontal elements typically consist of diaphragms, including collectors. Diaphragms transmit inertial forces from the floor system to the vertical elements of the seismic force-resisting system.
They also tie the vertical elements together and thereby stabilize and transmit forces among these elements as may be required during earthquake shaking. Diaphragms are thus an essential part of the seismic force-resisting system and require design attention by the structural engineer to ensure the structural system performs adequately during earthquake shaking. The horizontal elements can consist of truss elements or horizontal diagonal bracing and diaphragms are constructed as essentially solid, planar elements made of wood, steel, concrete or combinations of these. Fig. 1. Isometric view of a basic building structural system comprising diaphragms, walls and frames, and foundation 1. 1Diaphragms Diaphragms serve multiple roles to resist gravity and lateral forces in buildings (Fig. 1. 2). They include: •Resist gravity loads. •Provide lateral support to vertical elements against buckling, and tie these together so that they complete the three-dimensional framework to resist lateral loads. •Resist out-of-plane forces developed by the exterior walls and cladding as a building responds to an earthquake, and also by the wind pressure acting on exposed wall surfaces. Resist large horizontal thrust from inclined columns, acting within the plane of the diaphragms due to gravity and overturning actions. •Transfer lateral inertial forces to vertical elements of the seismic force-resisting system. •Transfer lateral shears through the diaphragm one vertical element of the seismic force-resisting system to another (especially at discontinuities in the vertical elements). •Support soil loads below grade – For buildings with subterranean levels, soil pressure bears against the basement walls ut-of-plane. The basement walls span between diaphragms, producing compressive reaction forces at the edge of the diaphragms. Fig. 1. 2 Roles of diaphragms 1. 2 Collectors Collectors are tension and compression elements that gather (collect) shear forces from diaphragms and deliver the force to vertical elements. Collectors also deliver forces from vertical elements into the diaphragm as shown in Fig. 1. 3. This type of collector, referred to as a distributor, is required where forces are redistributed among vertical elements.
Collectors can be in the form of beams or a zone of reinforcement within a slab such as shown in Fig. 1. 4. Wide sections of slabs used as collectors are referred to as distributed collectors. Fig. 1. 3 Distributor Fig. 1. 4 Collectors (Plan) In some cases, tension and compression collectors can be fit within the width of the wall, in which case all the tension and compression force is transferred into the wall at the wall boundary. In this case, only uniform diaphragm shear is transferred through shear-friction to the side of the wall.
In other cases, the collector has to be wider than the width of the wall, so only part of the collector force is transferred directly into the wall boundary, with the rest being transferred through shear-friction to the side of the wall. Significant force transfer often occurs at ground level slabs over one or more basements. At these slabs, forces are distributed out of vertical elements such as shear walls and transferred through the diaphragm to the basement walls.
The flexibility of the diaphragm will greatly reduce the force that is distributed out of the walls, thus reducing the backstay effect. It will also reduce the backstay effect of the shear walls extending below the ground level. The force couple resisting overturning in walls at the podium level and below is known as the backstay effect. Fig. 1. 5 Backstay effect CHAPTER 2 BUILDING CODE REQUIREMENT This paper is based on the following codes: •Uniform Building Code (UBC) 1997 •ACI 318-08
The seismic design requirements for collector elements are addressed in 1997 UBC as follows: “Collector elements shall be provided that are capable of transferring the seismic forces originating in other portions of the structure to the element providing the resistance to those forces. Collector elements, splices and their connections to resisting elements shall resist the forces determined. In addition, collector elements, splices, and their connections to resisting elements shall have the design strength to resist the combined loads resulting from the special seismic load. The “Special Seismic Load Combinations” includes the estimated “Maximum Earthquake Force”, Em, which is defined as the basic seismic design force multiplied by an overstrength factor, ? o. The intent of the ? o –amplification factor is to allow for the likely overstrength of the vertical seismic force- resisting elements so that major yielding does not occur in collectors and their connections prior to yielding and inelastic response at the vertical elements of the building’s seismic-force-resisting system. Applying the system overstrength factor per 1997 UBC effectively increases the collector load demand by approximately 200% to 300%.
It often becomes impractical to provide a collector element that is concentric with the shear wall/moment frame that has adequate strength to resist the full seismic force and transfer it to the ends of the vertical seismic-force resisting element. Additionally, by concentrating all the collector reinforcement in a small region in line with the wall, the elastic stiffness of the adjacent floor slab may be underestimated. This traditional methodology can result in a condition where the floor slab having larger area and being stiffer than the collector element, would initially resist the collector seismic tension.
If the floor slabs are not adequately reinforced for the seismic tension force, significant cracking may occur, until the reinforced collector element starts yielding and reaches its full strength. 2. 1 Illustration Of Methodology The purpose of this discussion is to illustrate an alternative collector design approach where part of the seismic load is resisted by the reinforcement directly in line with the shear wall, which transfers the force directly to the end of the shear wall.
The balance of seismic force is resisted by reinforcing bars placed along the sides of the wall and uses the slab shear-friction capacity at the wall to- slab interface to transfer seismic forces to the wall (Fig. 2. 1). (Shear wall is used to represent vertical seismic force-resisting element, the condition for moment frames or other systems are similar). Fig. 2. 1 Perspective view of wall and collector It is noted that where the slab is adjacent to a shear wall, and is used to resist seismic collector forces, there is an eccentricity between the resultant of collector force in the slab and shear wall reaction.
This eccentricity can create secondary stresses in the slab transfer region (or diaphragm segment) adjacent to the wall. For a complete and consistent load path design, the effect of seismic force eccentricity in this diaphragm segment must be checked to determine that adequate reinforcement is provided to resist the induced stresses. A key design issue in this approach is to determine the effective width of slab adjacent to the shear wall that is used to resist collector forces.
Where a narrow effective width is assumed, eccentric force effects become small, but more reinforcement may be required to drag the collector forces in-line with the wall. On the other hand, if a wide slab width is used as collector, more force can be transferred through the slab, reducing reinforcing bar congestion at the end of the wall; however, secondary stresses caused by force eccentricity would be larger. CHAPTER 3 COLLECTOR DESIGN PROCEDURE The following is a suggested outline for collector design procedure. 1.
Determine the collector design forces Determine the seismic forces distribution to the vertical seismic force-resisting members by conventional analysis. 2. Determine the steel area directly in line with shear wall It is proposed that the section of the collector that is directly in line with the wall be designed for all the applicable gravity load demand plus a reasonable portion of the total collector force selected, considering the required number of reinforcing bars and practical limitations of reinforcing bar congestion at the end of the wall.
The balance of the collector force will need to be resisted by the adjacent slab section in accordance with the following design procedure. 3. Select effective slab width to resist collector forces The following equation is used to assign an assumed effective slab width: (3. 1) where, t – thickness of the wall L – length of the wall. 4. Determine required steel area to resist collector tension Determine the net tension force, TNET, and the required steel area, AS, at each section along the collector. The required steel area is calculated only at the maximum force location). For most reinforced concrete slabs the net tension force is equal to the calculated collector tension, Ft. (3. 2) where, ? – capacity reduction factor as per UBC fy – yield strength of reinforcing steel. The reinforcing area, AS, represents the total area of the required reinforcing steel. Part of this steel may be placed in the slab element directly in-line with the wall and the balance may be distributed throughout the effective slab width adjacent to the wall.
The collector reinforcement shall be placed, as much as practicable, symmetrically about the centroid of the concrete section in order to prevent additional out-of-plane slab bending stresses. 5. Check collector compressive stress Determine the total compression force, CNET, and check concrete compressive stress at each section along the collector. (Concrete compressive stress is checked only at the maximum force location). For most reinforced concrete slabs the total compression force is equal to the calculated collector compression, Fc.
As per 1997 UBC design concept for collectors in compression: “Structural-truss elements, struts, ties and collector elements with compressive stress exceeding 0. 2f’c shall have special transverse reinforcement over the total length of the element. The special transverse reinforcement may be discontinued at a section where the calculated compressive stress is less than 0. 15f’c. Stresses shall be calculated for the factored forces using a linearly elastic model and gross-section properties of the elements considered. ” The Concrete Subcommittee interprets that the 0. f’c stress criterion should apply to collector forces before they are magnified by the ? o factor. If ? o-magnified forces are used, then the 0. 2f’c criterion becomes 0. 45f’c for consistency with the intent of the UBC and established collector design practices. The limit of 0. 45 was selected based on the following arithmetic: 0. 2 (? o = 2. 2 ~ 2. 8) = 0. 44 ~ 0. 56 Hence: (3. 3) where, CNET – the total compression force AC – gross cross-sectional area of the effective concrete section in compression. 6. Check diaphragm segments for eccentricity
For conditions where all or part of collector reinforcement is placed at the sides of the shear wall, the transfer region (or the diaphragm segment adjacent to the wall) should be designed to resist the seismic shear and in-plane bending moment resulting from the eccentricity of the portion of collector force that is not transferred directly into the end of the shear wall. In keeping with the code intent to design collectors and their connections for the maximum expected seismic force, Em, the stresses due to collector eccentricity in that diaphragm segment adjacent to the wall shall be determined using an overstrength amplification factor, ? . Fig. 3. 1 shows an idealized partial plan at the edge of a diaphragm with the seismic resisting wall “a-d” and the seismic collector located eccentrically at a distance “e” relative to the wall. The figure also shows the diaphragm segment adjacent to the wall with internal forces acting on the free-body “abcd”, (tension/compression forces perpendicular to the free-body diagram are ignored for the sake of simplicity). Fig. 3. 1 Diaphragm segment plan
The collector design force is designated as FC and in a general sense it consist of compression and tension collector portions and the portion of diaphragm shear force along line bc, respectively, designated as (FC)comp, (FC)tens, and Vd. (3. 4) Considering the seismic amplification factor and collector eccentricity, the maximum eccentric moment acting on the free-body abcd is calculated as: (3. 5) The applied eccentric moment should be resisted by the combined action of all the diaphragm internal forces, thus: (3. 6) here, the magnitude of internal forces, Ve, M1, M2, M3, could be calculated in a rigorous analysis in accordance with their relative stiffness. The moment capacity of the slab region under direct tension from collector force, i. e. moment M3 in the Fig. 3. 1, may be conservatively neglected. Furthermore, the shear capacity Ve shall be calculated using only the capacity of shear reinforcing bars and neglecting the contribution of concrete section under tension. Hence, the strength limits for the shear force Ve, and bending moment M2, are determined as: (3. 7) (3. 8) where,
AS2 – the reinforcement areas perpendicular to section ab (je) – the effective moment arm and, Asv – the smaller of the reinforcing bar area parallel to sections ab and dc. Then, the required flexural strength, M1, can be calculated as: (3. 9) For conditions where the eccentricity, e, is small relative to the dimension h, it is reasonable to assume that the relative stiffness associated with the actions M1 and Ve is much larger than the other actions; hence, without being too conservative, the contribution of the moments M2 and M3 may be neglected, which simplifies the equation for M1, to the following: (3. 0) The required moment capacity, M1, can be computed by taking into account the effect of the slab’s distributed reinforcement that is provided for gravity loads, but is in excess of what is needed to resist seismic load combinations. For cases where the available distributed reinforcement is not adequate to satisfy the required strength, supplemental reinforcing steel should be provided at the eccentric force transfer zone. Fig. 3. 2 shows an arrangement of various reinforcing bars perpendicular to section bc and illustrates the terms used in the following computation for moment M1.
Fig. 3. 2 Diaphragm Segment Reinforcement (3. 11) where, AS1 – the available area of the distributed slab reinforcement perpendicular to the section bc that can be used for seismic load combination (j1h) – its effective moment arm AS* – the area of supplemental reinforcement and, (j*h) – the effective moment arm of the supplemental steel. 7. Check diaphragm segment shear strength The slab shear stress demand should be checked for the shear force transfer region adjacent to the wall and, where required, additional reinforcement shall be provided.
Two shear force transfer mechanisms should be considered. First, slab shear strength should be evaluated in accordance with UBC and considering the contribution of all available slab reinforcement. It should be noted that the common diaphragm proportions and support layout often create a condition that the diaphragm shear strength is less than the shear corresponding to the nominal flexural strength. Thus the strength reduction factor, ? , for shear should be taken as 0. 60 according to 1997 UBC. (3. 12) where,
Acv – the net area of the concrete section bounded by the slab thickness and length of the wall ? c – the ratio of the width to length of the diaphragm segments, which in this case is equal to effective slab width to the length of the wall and, ? n -the ratio of area of distributed shear reinforcement to gross concrete area perpendicular to that reinforcement. 8. Check shear-friction at wall-to-slab interface The strength of transfer mechanism by shear friction at the face of the supporting wall and/or frame should be checked.
For this mechanism the potential sliding plane should be identified; for most practical design cases the potential sliding plane is taken as the vertical plane at the interface between the wall and the slab. In accordance with the requirements of 1997 UBC, the shear friction reinforcement can include all reinforcement that crosses this plane, as long as it is not used to resist direct tension. Hence, the area of the required shear transfer reinforcement, AVF per foot of wall length is calculated as: (3. 13) where,
Vn – nominal shear strength ? – coefficient of friction given by 1. 0? , where ? = 1. 0 for normal weight concrete and 0. 75 for lightweight concrete Lw – length of interface between the wall and the slab. CHAPTER 4 CONSTRUCTABILITY ISSUES •Post cracking performance Planar elements such as shear walls and diaphragm slabs have a better post-cracking behavior if the reinforcing is reasonably distributed over regions of high shear and axial stress rather than being concentrated in narrow groups near the edges of these elements.
Distributed reinforcing allows the formation of multiple narrow cracks over the stressed region, while the stiffening effect of concentrated group reinforcing results in a few wide cracks with possible localized spalling. The current shear wall provisions allow and encourage the use of vertical reinforcing distributed over the wall section rather than in concentrated boundary elements. Similarly, provision of distributed steel in an assigned effective width of a collector element can result in better post cracking performance than if the collector is made up of large diameter bars in and closely adjacent to he vertical lateral force resisting element. •Collector reinforcement Collector and chord reinforcement is often located in the mid-depth of the slab. ACI 318 requires minimum centre-to-centre spacing of three longitudinal bar diameters, but not less than 1-1/2 in. and a minimum concrete clear cover of two and one-half longitudinal bar diameters, but not less than 2 in. Connections of collector reinforcement to vertical elements of the seismic force-resisting system are often congested regions.
In many cases, numerous large diameter bars are required to be developed into confined boundary zones of shear walls as shown in Fig. 4. 1. Designers should study these connections in detail to ensure adequate space exists. In many cases, increased slab thickness or beams are required to accommodate reinforcement detailing at the connections. Fig. 4. 2 shows where a beam was created to accommodate the collector reinforcement. Designers should also consider the slab depth provided where large collectors intersect.
Multiple layers of large diameter reinforcing bars can result in excessive congestion. Similarly, designers should be aware of locations where collectors intersect concrete beam longitudinal reinforcement. Fig. 4. 1 Collector connection to shear wall boundary zone Fig. 4. 2 Beam for large collector •Shear transfer Shear transfer between diaphragms and vertical elements of the seismic force-resisting system can be accomplished in a number of ways. Shear-friction reinforcement can be provided for transfer of forces along the length of the vertical element.
For cases where the vertical elements of the seismic force-resisting system are cast in advance of the slabs, or vice versa, the use of shear keys should be considered in order to achieve a coefficient of friction, ? , of 1. 0. Compressive collector forces can be transferred via direct bearing at wall ends. An appropriate effective slab bearing area should be considered, and compressive stresses in the slab should be evaluated to determine if confinement is required. Tensile forces can be transferred through collector reinforcement that is developed in both the diaphragm and the vertical element.
The length of tension collectors within the diaphragm should consider the assumed shear stress distribution as well as the shear strength of the diaphragm. The length within the vertical element must be sufficient to fully transfer the force to the vertical element. •Location of construction joints Construction joints create weakened planes within a diaphragm. Shear-friction reinforcement can be provided across construction joints if necessary to maintain continuity of the diaphragm in shear. CHAPTER 5 CONCLUSION
This paper presents a methodology on the development and use of reinforced concrete slabs as seismic collectors, based on the 1997 Uniform Building Code and ACI 318-08. The design is done for an estimated maximum earthquake force, Em (basic seismic design force, Eh, multiplied by an overstrength factor, ? o). It is assumed that the actual maximum seismic load will not greatly exceed ? oEh and that the collector steel has not been elongated by strains beyond the tension yield stress fy since it has been designed to resist tension force ? oEh with stress equal or less than ? fy. REFERENCES . Jack P. Moehle, John D. Hooper, Dominic J. Kelly, Thomas R. Meyer, “Seismic design of cast-in-place concrete diaphragms, chords and collectors”, NEHRP Seismic Design Technical Brief No. 3, 29 pp, August 2010. 2. SEAOC (2005), “Design of concrete slabs as seismic collectors,” Seismology and Structural Standards Committee, Structural Engineers Association of California, 15 pp. (http://www. seaoc. org/seismpdfs/Positions/0505_Concreteslabs. pdf) 3. ACI (2008). Building code requirements for structural concrete (ACI 318-08) and commentary, American Concrete Institute, Farmington Hills, MI.