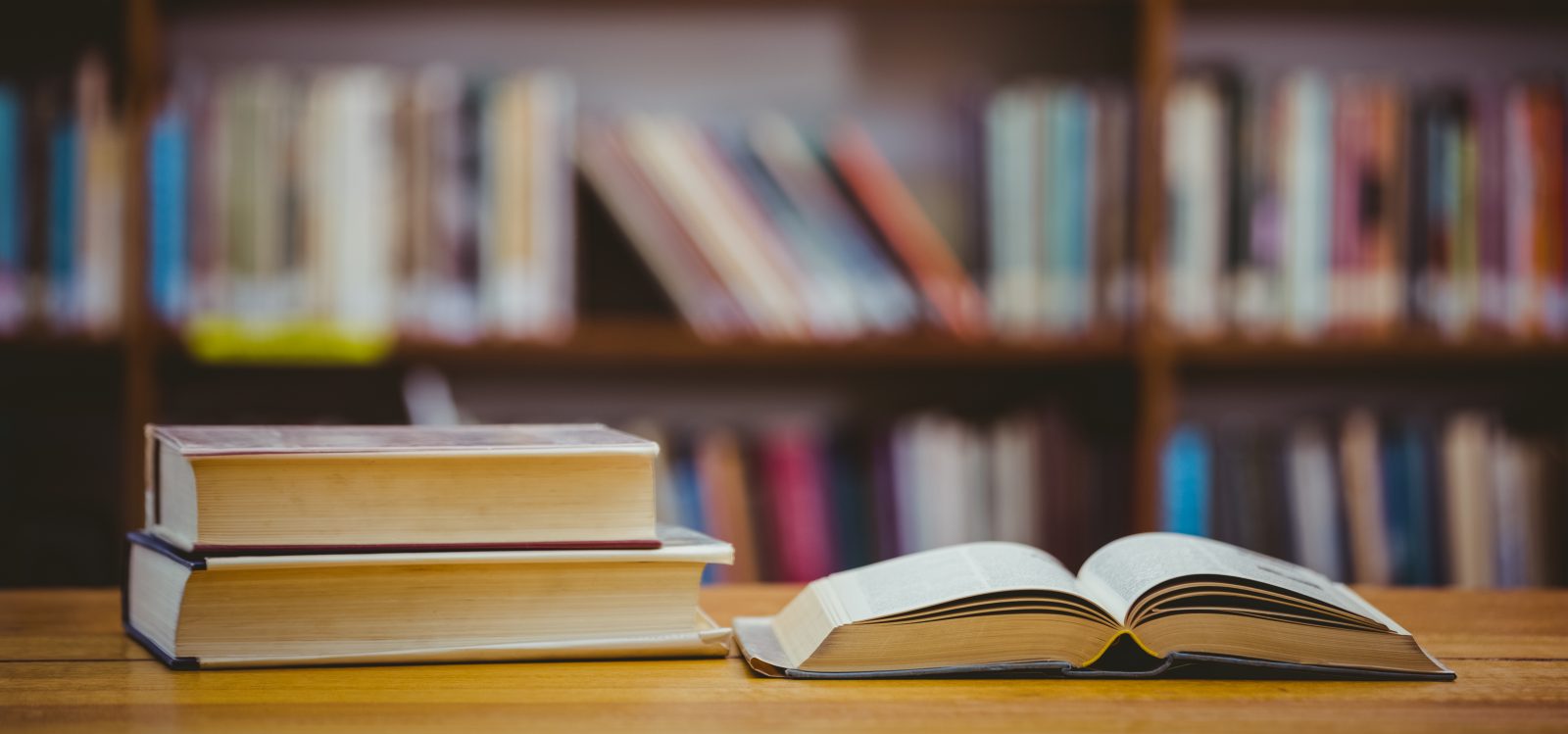
Project Title: Investigation of health, safety and environmental hazards in the lime burning industry in Uganda A case study of Nomson Lime Limited By KAAYA JOSEPH (+256774560185,maghanjoe@yahoo. co. uk) ACKNOWLEDGMENTS: To all who have encouraged and helped me throughout the period of carrying out my final year project, I wish to extend my appreciation to my supervisor and co-supervisor Mr. Kasedde Hillary and Dr. Adam Sebbit respectively who continuously guided me throughout the entire period.
I wish to extend my sincere gratitude to the management and the staff of Nomson Lime Limited who allowed me to carryout my research from there. I also extend my appreciation to my parents Mr. and Mrs. Kizito who financially supported me in order to successfully complete my project. I also extend my appreciation to my brothers, sisters and friends who advised me during the period of carrying out my project, not forgetting Sophie, Dr. Hawa, and Michael Joel. May the almighty God bless you. DEDICATION: I would like to dedicate this report to my parents Mr. nd Mrs. Kizito who have endeavored to support me up to the end of my studies. LIST OF ABBREVIATIONS: [pic] Calcium Carbonate CaO Calcium Oxide (Quick lime) Ca [pic] Calcium Hydroxide (Hydrated lime) [pic] Methane CO Carbon monoxide [pic] Carbon dioxide EHS Environmental, Health and Safety HCL Hydrogen chloride HF Hydrogen fluoride MSD Musculoskeletal disorder MSDS Material Safety Data Sheets [pic] Nitrous oxide [pic] Nitrogen oxides
OHS Occupational Health and Safety OSHA Occupational Safety and Health Administration (United States) PCBs Polychlorinated biphenyls PCDDs Polychlorinated dibenzodioxins PCDFs Polychlorinated Dibenzofurans PM particulate matter PPE Personal Protective Equipment [pic] Sulphur oxides VOC Volatile organic compounds LIST OF FIGURES Figure 1: Lime burning kiln at Nomson lime limited1 Figure 2: Sieving Process at Nomson Lime Limited3 Figure 3: process scheme for Lime burning26
Figure 4: process flowchart for Lime burning27 Figure 5: % contributions of hazards at Nomson Lime ltd42 Figure 6: contributions of each hazard44 Figure 7: Calcining process46 Figure 8: Workers at Nomson pushing the Firewood logs to charge the kiln47 Figure 9: Bagging process at Nomson47 Figure 10: Sieving process at Nomson48 Figure 11: Pie chart showing the Health hazards contributions49 Figure 12: Limestone crushing at Nomson50 Figure 13 : Grinding machine at Nomson Lime Ltd51 Figure 14: safety hazards and their contributions51 Figure 15: Kiln offloading process at Nomson52
Figure 16: Calcination process emissions to the environment53 Figure 17: Smoke laden atmosphere at Nomson during Lime burning operation53 Figure 18: Environmental hazards and their contributions54 LIST OF TABLES Table 1: Lime burning processes, events and their respective outcomes. 29 Table 2: Probability of Occurrence Ranking Factors34 Table 3: Numerical Values and Definitions for Impacts on health, safety and Environment35 Table 4: Probability of Occurrence Ranking for Hazards of Concern36 Table 5: Ranking of Hazards of concern37 Table 6: Total Risk Ranking Value for Hazards of Concern40
Table 7: Hazard Ranking Results for Hazards of Concern41 ABSTRACT This study assesses the health, safety and environmental hazards in the lime burning industry in Uganda, taking a case study of Nomson Lime Limited. Key issues of concern here are: • The potentially hazardous manufacturing processes used in the lime burning industry. • The little emphasis put to the health, safety and environmental hazards involved. • Lack of proper statistics and detailed documentation regarding the area of OHS practices yet the people involved seemed to be so concerned.
These issues were tackled through various methods which included; Literature Review, Data Collection, documentation of the lime burning process/ flow line at Nomson, Risk Assessment, Data Analysis, Documentation of the whole project; From the findings and discussions, it was concluded that proper occupational health, safety and environmental practices are neglected at Nomson Lime Limited. The following recommendations that will help to improve lime burning operations (OHS practices) in Tororo were generated: 1. The forceful use of appropriate Personnel Protection Equipment is recommended.
Special attention has to be paid to skin protection, eye protection, and protection of the respiratory system. 2. In the short term, engagement of operators in industry safety initiatives and forums in order to share knowledge and good practices so that these become the industry ‘norm’. Publish safety data using common metrics to encourage comparison and benchmarking among companies. 3. In the medium to long term, the industry should encourage the wider use of risk assessment in plant design, plant modification and for key operational activities. 4.
Adopt best practice in emission control measures and promulgate their use in all areas of operation. Special attention has to be paid to skin protection, eye protection, and protection of the respiratory system. 5. There is an urgent need to design programmes at industry, national and international levels to raise the understanding of the implications of Lime burning on a continuing basis. 6. Governments, professional bodies and research organizations need to take an active role in providing information and in promoting awareness among the public. 7.
Since sustainable development requires a change in consumption patterns towards more environment friendly products and a change in investment patterns to encompass long? term needs, governments will have to formulate effective legislation and ensure adequate expenditure on research, dissemination of information and enforcement 8. Future work should involve a detailed experimental investigation of the lime burning process on the health, safety and environmental hazards in lime burning industry in Uganda. Table of Contents CHAPTER ONE: INTRODUCTION1 1. 0Background1 1. 1 Problem Statement:3 1. 2 Objectives4 1. 2. 1 Main Objective:4 . 2. 2 Specific objectives:4 1. 3 Justification of the Study:4 1. 4 Scope of the project5 1. 5 Expected outcomes5 CHAPTER TWO6 LITERATURE REVIEW6 2. 0 Introduction6 2. 1 Reasons for Occupational health and safety6 2. 2 Hazards, risks, outcomes7 2. 3. 1 Process description9 2. 3. 2 Techniques10 2. 3. 3 Emissions10 2. 3. 4 Controls12 2. 4. 0 Environmental, Health, and Safety Guidelines for Lime Manufacturing12 2. 4. 1 Environment13 CHAPTER 3:22 METHODOLOGY22 3. 0 Introduction22 3. 1 Literature Review22 3. 2 Data Collection22 3. 3 Technical Description of the lime burning process/ flow line23 3. 4 Identification of Hazards23 . 5 Risk Assessment23 3. 6 Data Analysis23 3. 7 Documentation23 Milestones24 CHAPTER FOUR:25 Results and Discussions25 4. 1 Technical Description of the Lime burning process:25 4. 1. 1 Crushing the stones25 4. 1. 2 Charging of the kilns25 4. 1. 3 Calcinations25 4. 1. 4 Offloading26 4. 1. 5 Hydration26 4. 1. 6 Sieving26 4. 1. 7 Grinding26 4. 1. 8 Bagging/ packing26 4. 2 Identification of Health, safety and Environmental hazards29 Existing Remedies34 Critical accidents that have ever occurred at the site34 4. 3 Risk Assessment35 4. 3. 1 Hazard Ranking Methodology35 4. 3. 1. 1 Probability of Occurrence35 4. 3. 1. Impact35 4. 3. 2 Risk Ranking Value36 4. 3. 3 Hazard Ranking Results36 5. 1 Health, Safety and Environmental implications47 5. 1. 1 Health47 5. 1. 2 Safety51 5. 1. 3 Environmental53 5. 2 Key Constraints to Promoting Practical Strategies for Control of Hazards in the Lime Burning Industry55 5. 2. 1 Insufficient information55 5. 2. 2 Inadequate Public Awareness55 5. 2. 3 Differences in perception of risks56 5. 2. 4 Conflict of interest56 5. 2. 5 Challenges for Company Management56 5. 2. 6 Inadequate regulatory mechanisms56 5. 2. 7 Inadequate collaboration57 5. 2. 8 Additional considerations for developing countries57
CHAPTER SIX58 Conclusion and Recommendations58 6. 0Introduction58 6. 1Conclusion58 References60 CHAPTER ONE: INTRODUCTION Background Lime burning in Tororo district is carried out on a small and medium scale basis by enterprises that use the traditional vertical shaft kilns and batch pit kilns which are poorly constructed, leaving a lot of room for heat loss and escape of dangerous fumes that pose a great risk to the people. The interaction of these factors and humans occurs either by absorption through the skin, by intake into the digestive track via the mouth, or by inhalation into the lungs.
The results of the interaction can be harmful to human health in a variety of ways, including: respiratory diseases such as asthma, heart diseases, cancer, brain damage or poisoning. The effects of the hazards may be slow, cumulative, irreversible, and complicated by non? occupational factors. (Sebbit et al, 2009). Lime is produced via the calcination of high calcium limestone (calcium carbonate) or other highly calcareous materials such as aragonite, chalk, coral, marble, and shell; or via the calcination of dolomitic limestone.
Calcination occurs in a high temperature furnace called a kiln, where lime is produced by heating the limestone to about 2000° F, driving off carbon dioxide in the process. Dead burned dolomite is a type of dolomitic lime produced to obtain refractory characteristics in the lime. The kiln is the heart of the lime manufacturing plant, where various fossil fuels (such as coal, petroleum coke, natural gas, and fuel oil) are combusted to produce the heat needed for calcination. Various health, safety and environmental hazards originate from the lime burning process and the disposal of related wastes in Uganda.
As a result of the Cement Factory ceasing lime production, locally operated kilns emerged. Production from the kilns is not well known since each individual operates almost independently with production being very much influenced by demand, and little attention given to the rudimentary methods used. Atmospheric emissions in the lime manufacturing industry include particulate emissions from the mining, handling, crushing, screening and calcining of the limestone and emissions of air pollutants generated during fuel combustion in kilns.
These emissions are not very significant on a global or even regional scale. However, lime works can be an important emission source of air pollutants on a local scale. The production of lime causes emissions from both processes and combustion. Some of the harmful conditions include; flying stones during the sizing and crushing of the stones, heavy firewood logs that hit the people during charging process of the kilns, inhalation of dust particles mainly during the sieving process, excessive heat from the kilns during the burning process, potential damage to the skin, accidents due to collapse of the kilns.
The crude methods used in the extraction of the limestone from the quarries also pose high safety risks to the people and the environment through noise pollution and air pollution. (EMEP/EEA emission inventory guidebook 2009) The fuels used in the burning processes for example firewood, together with the poor technology kilns leave the environment at a great risk thereby exposing the persons around to dangerous consequences. The kilns have cracks in them so there is a lot of escape of the dangerous fume and fuels to the environment.
There was no detailed documentation regarding this area yet the people involved seemed to be so concerned. There was hence a need to investigate the involved health, safety and environmental hazards and hence ensuring a sustainable production process. 1. 1 Problem Statement: Uganda has a variety of locally operated kilns; for example in Tororo district where, lime burning is carried out on a small and medium scale basis by enterprises that use the traditional vertical shaft kilns and batch pit kilns which seem to be inefficient in their high energy usage and the many hazards involved.
Production is mainly influenced by demand with little emphasis put to the health, safety and environmental hazards involved. Figure 2: Sieving Process at Nomson Lime Limited The lime manufacturing industry is labor intensive and uses potentially hazardous manufacturing processes. The industry experiences high accident rates but no clear statistics have been documented which has for a long time led to lack of follow- up. These hazardous processes impact on those working within the industry, although health hazards also impact on local communities.
Workers are also at risk from hazards common to many industrial working environments: general slips, trips and falls, machinery hazards and electrical hazards. This study seeks to find possible solutions to the hazardous events. There was no detailed documentation regarding this area yet the people involved seemed to be so concerned due to the rudimentary processes that have got longtime health effects to the lives of the personnel in the lime burning process which implied that ameliorative measures had to be considered in order to curb this situation. 1. 2 Objectives 1. 2. 1 Main Objective:
The broad objective of this project was to improve the OHS practices in the lime burning industry through assessment of the key health, safety and environmental hazards and bridging the gap. 1. 2. 2 Specific objectives: ? To assess the lime burning processes used at Nomson in order to obtain an overview of the current OHS practices in the lime burning industry ? To benchmark the current lime burning process at Nomson with health, safety and environmental legal frameworks and regulations in lime burning through conducting risk assessment procedures, environmental, health and afety assessment. ? To generate information that will be vital in giving recommendations that will help to improve lime burning operations in Tororo. 1. 3 Justification of the Study: The health, safety and environmental hazards in the lime burning industry of Uganda had really become a menace due to the vast amount of dangers which they posed not only to the people involved but also to the environment around.
Exposure to these compounds has been demonstrated to cause adverse health effects when present in concentrations higher than those typically found in ambient air. Therefore, to be able to curb down these dangers, a baseline assessment needed to be done in order to avail the required information since there was a problem of lack of well documented information about the whole idea. This research was therefore of paramount importance in finding solutions to hazards involved in lime burning industry in Uganda.
Despite the fact that the extent to which these adverse health effects occurred in the populations surrounding these facilities was not known, the project aimed at reducing these emissions and subsequent exposures. The people involved seemed to be so concerned due to the rudimentary processes had longtime health effects to the lives of the personnel in the lime burning process and no fruits could be achieved with no detailed documentation regarding this area yet which implied that ameliorative measures had to be considered in order to curb this situation.
This project also generated useful information that will help to enlighten the community (public), government and governmental institutions, non-governmental organizations, company shareholders, scholars, and company lenders on the benefits that can be got from application of occupational health and safety in the lime burning industry. The study came up with mitigation and preventive measures aimed at ensuring a safe and eco-friendly lime burning process. 1. 4 Scope of the project
This project focused on Investigation of health, safety and environmental hazards in the lime burning industry in Uganda, taking a case study of Nomson Lime Limited in Tororo district. This industry is located along the Tororo-Kampala highway opposite Tororo Cement Industries and within Usukuru hills complex where the limestone is quarried. 1. 5 Expected outcomes • To ascertain the extent of the hazards involved in the lime burning industry in relation to OHS practices. To bridge the missing gap in the current lime producing processes in Uganda as compared to compliance with health, safety and environmental legal frameworks and regulations in lime burning. • To come up with a list of possible recommendations that could be adopted by the small scale lime burners as a way of ensuring a safe and eco-friendly lime burning process. CHAPTER TWO LITERATURE REVIEW 2. 0 Introduction Occupational health and safety is a cross-disciplinary area concerned with protecting the safety, health and welfare of people engaged in work or employment.
The goal of all occupational health and safety programs is to foster a safe work environment. As a secondary effect, it may also protect co-workers, family members, employers, customers, suppliers, nearby communities, and other members of the public who are impacted by the workplace environment. It may involve interactions among many subject areas, including occupational medicine, occupational (or industrial) hygiene, public health, and safety engineering, chemistry, and health physics. 2. 1 Reasons for Occupational health and safety
The event of an incident at work (such as legal fees, fines, compensatory damages, investigation time, lost production, lost goodwill from the workforce, from customers and from the wider community. Legal – Occupational requirements may be reinforced in civil law and/or criminal law; it is accepted that without the extra “encouragement” of potential regulatory action or litigation, many organizations would not act upon their implied moral obligations. Occupational health and safety officers promote health and safety procedures in an organization.
They recognize hazards and measure health and safety risks, set suitable safety controls in place, and give recommendations on avoiding accidents to management and employees in an organization. This paper looks at the main tasks undertaken by OHS practitioners in Europe, Australia and the United States of America, and the main knowledge and skills that are required of them. “Like it or not, organizations have a duty to provide health and safety training. But it could involve much more than you think. ” (Damon, Nadia. 2008. ‘Reducing the Risks’, Training and Coaching Today, United Kingdom, pg. 14)
An effective training program can reduce the number of injuries and deaths, property damage, legal liability, illnesses, workers’ compensation claims, and missed time from work. A safety training program can also help a trainer keep the required OSHA-mandated safety training courses organized and up-to-date. Safety training classes help establish a safety culture in which employees themselves help promote proper safety procedures while on the job. It is important that new employees be properly trained to embrace the importance of workplace safety as it is easy for seasoned workers to negatively influence the new hires.
That negative influence however, can be purged with the establishment of new, hands-on, innovative effective safety training which will ultimately lead to an effective safety culture. A 1998 NIOSH study concluded that the role of training in developing and maintaining effective hazard control activities is a proven and successful method of intervention. 2. 2 Hazards, risks, outcomes The terminology used in OSH varies between states, but generally speaking: A hazard is something that can cause harm if not controlled. The outcome is the harm that results from an uncontrolled hazard.
A risk is a combination of the probability that a particular outcome will occur and the severity of the harm involved. “Hazard”, “risk”, and “outcome” are used in other fields to describe e. g. environmental damage, or damage to equipment. However, in the context of OSH, “harm” generally describes the direct or indirect degradation, temporary or permanent, of the physical, mental, or social well-being of workers. For example, repetitively carrying out manual handling of heavy objects is a hazard. The outcome could be a musculoskeletal disorder (MSD) or an acute back or joint injury. The risk can be expressed numerically (e. . a 0. 5 or 50/50 chance of the outcome occurring during a year), in relative terms (e. g. “high/medium/low”), or with a multi-dimensional classification scheme (e. g. situation-specific risks). 2. 2. 1 Hazard Assessment Hazard analysis or hazard assessment is a process in which individual hazards of the workplace are identified, assessed and controlled/eliminated as close to source (location of the hazard) as reasonable and possible. As technology, resources, social expectation or regulatory requirements change, hazard analysis focuses controls more closely toward the source of the hazard.
Thus hazard control is a dynamic program of prevention. Hazard-based programs also have the advantage of not assigning or impling there are “acceptable risks” in the workplace. A hazard-based program may not be able to eliminate all risks, but neither does it accept “satisfactory” — but still risky—outcomes. And as those who calculate and manage the risk are usually managers while those exposed to the risks are a different group, workers, a hazard-based approach can by-pass conflict inherent in a risk-based approach. 2. 3 Lime production process:
Lime is produced by burning [pic] or (less frequently) dolomite (calcium and magnesium carbonate), providing sufficient heat to reach temperatures of above 800°C and cause decarbonation of the raw material to produce calcium oxide (CaO, known as quicklime). The quicklime is then maintained at temperatures of 1,200-1,300°C, to adjust reactivity. The burned lime can be delivered to the end user in the form of quicklime (hard, medium, and soft burned, based on their reactivity). Soft burnt lime is the most reactive and commonly employed by steel.
There are many synonyms for lime, the main ones being quicklime and its chemical name, calcium oxide. High calcium lime consists primarily of calcium oxide, and dolomitic lime consists of both calcium and magnesium oxides. Lime is produced via the calcination of high calcium limestone (calcium carbonate) or other highly calcareous materials such as aragonite, chalk, coral, marble, and shell; or via the calcination of dolomitic limestone. Calcination occurs in a high temperature furnace called a kiln, where lime is produced by heating the limestone to about 2000° F, driving off carbon dioxide in the process.
Dead burned dolomite is a type of dolomitic lime produced to obtain refractory characteristics in the lime. The kiln is the heart of the lime manufacturing plant, where various fossil fuels (such as coal, petroleum coke, natural gas, and fuel oil) are combusted to produce the heat needed for calcination. There are five different types of kilns: rotary, vertical, double shaft vertical, rotary hearth, and fluidized bed. The most popular is the rotary kiln, but the double-shaft vertical Kiln is an emerging new kiln technology gaining in acceptance because of its energy efficiency.
Rotary kilns may also have preheaters associated with them to improve energy efficiency. As discussed further in this preamble, additional energy efficiency is obtained by routing exhaust from the lime cooler to the kiln, a common practice. Emissions from lime kilns include, but are not limited to, metallic HAP, HCl, PM, sulfur dioxide, nitrogen oxides, and carbon dioxide. These emissions predominately originate from compounds in the limestone feed material and fuels (e. g. , metals, sulfur, chlorine) and are formed from the combustion of fuels and the heating of feed material in the kiln.
All types of kilns use external equipment to cool the lime product, except vertical (including double-shaft) kilns, where the cooling zone is part of the kiln. Ambient air is most often used to cool the lime (although a few use water as the heat transfer medium), and typically all of the heated air stream exiting the cooler goes to the kiln to be used as combustion air for the kiln. The exception to this is the grate cooler, where more airflow is generated than is needed for kiln combustion, and consequently a portion (about 40 percent) of the grate cooler exhaust is vented to the atmosphere.
We estimate that there are about five to ten kilns in the U. S. that use grate coolers. The emissions from grate coolers include the lime dust (PM) and the trace metallic HAP found in the lime dust. Lime manufacturing plants may also produce hydrated lime (also called calcium hydroxide) from some of the calcium oxide (or dolomitic lime) produced. Hydrated lime is produced in a hydrator via the chemical reaction of calcium oxide (or magnesium oxide) and water. The hydration process is exothermic, and part of the water in the reaction chamber is converted to steam.
A wet scrubber is integrated with the hydrator to capture the lime (calcium oxide and calcium hydroxide) particles carried in the gas steam, with the scrubber water recycled back to the hydration chamber. The emissions from the hydrator are the PM comprised of lime and hydrated lime. Operations that prepare the feed materials and fuels for the kiln and process the lime product for shipment or further on-site use are found throughout a lime manufacturing plant.
The equipment includes grinding mills, crushers, storage bins, conveying systems (such as bucket elevator, belt conveyors), bagging systems, bulk loading or unloading systems, and screening operations. The emissions from these operations include limestone and lime dust (PM) and the trace metallic HAP found in the dust. Atmospheric emissions in the lime manufacturing industry include particulate emissions from the mining, handling, crushing, screening and calcining of the limestone and emissions of air pollutants generated during fuel combustion in kilns.
These emissions are not very significant on a global or even regional scale. However, lime works can be an important emission source of air pollutants on a local scale. 2. 3. 1 Process description Two major types of processes can be considered within the lime work operations: quarrying, Crushing, and size grading of minerals; and combustion of fuels in lime kilns. Limestone quarries are usually developed in a number of benches or lifts. For primary blasting of the limestone, holes are made by drills operated by compressed air (Parker, 1978).
The excavated limestone is transferred for crushing and grinding. There are several types of crushing and grinding machines to produce limestone of sizes suitable for several designs of kilns. During the kiln operations the limestone reaches temperatures as high as 900 °C, and carbon dioxide is driven off limestone to leave so-called quicklime. The quicklime descends through the cooling zone and is discharged at the base of the kiln. Obviously, various air pollutants are generated during combustion of fuels in the kiln.
Hydrated lime is made by adding water to crushed or ground quicklime and thoroughly mixing the quicklime and the water. Milk of lime can be produced either by slaking quicklime with an excess of water or by mixing hydrated lime with water. 2. 3. 2 Techniques At present two major types of kilns are in use: vertical and rotary kilns. Because of larger size of charge material, lower air velocities and less agitation, vertical kilns emit lower amounts of particles but higher amounts of sulphur dioxide and carbon monoxide.
However, in recent years there have been important developments in the design and use of rotary kilns. They require a more carefully classified and smaller size of limestone than for the vertical kilns. 2. 3. 3 Emissions Pollutants released are sulphur oxides ([pic]), nitrogen oxides ([pic]), volatile organic compounds (Non-methane VOC and methane ([pic]), carbon monoxide (CO), carbon dioxide ([pic]), nitrous oxide (N2O) and particulate matter. According to CORINAIR90 the main relevant pollutants are[pic],[pic], CO and [pic] (Bouscaren, 1992).
Sulphur dioxide emissions are influenced by several factors, including the sulphur content of the fuel, the sulphur content and mineralogical form (metal sulphide such as pyrite, or sulphates such as gypsum) of the stone feed, the quality of lime being produced and the type of kiln. Due to variations in these factors, plant-specific [pic] emission factors are likely to vary significantly from the average emission factors presented here. The dominant source of sulphur emissions is the kiln’s fuel, particularly coal and petroleum derived coke, where the levels of sulphur may be as high as 5 % by weight.
The amount of sulphur present will vary widely according to the nature of the deposits used. During the calcining operation, sulphide and sulphates are decomposed to yield sulphur dioxide. On combustion of the fuel, the sulphur compounds present in the fuel are oxidized to sulphur dioxide and pass through the burning zone of the kiln with the exhaust gases (EPA, 1995; HSMO, 1992). When sulphur-containing fuels are burnt, for practical purposes sulphur in the kiln exhaust may be assumed to be emitted as sulphur dioxide, although there is usually some sulphur trioxide formed.
In the case of lime manufacture in shaft kilns, much of the sulphur re-combines with the burnt lime and the emissions of sulphur dioxide are subsequently reduced. In the case of rotary and rotating hearth kilns, combinations of process design and combustion conditions can be selected to ensure that most of the sulphur is expelled as sulphur dioxide in the kiln gases (HSMO, 1992). The oxides of nitrogen are produced through the reaction of the nitrogen and oxygen in the air and through the oxidation of the nitrogen compounds contained in the fuel.
There is a significant increase in the amount of oxides of nitrogen (mainly nitric oxide) which is formed at temperatures above 1,400 °C. The formation of nitric oxide is also a function of the excess air. When operating near to stoichiometric conditions in the kiln, there is localized generation of carbon monoxide. This acts as a reducing agent so that any nitric oxide which may be present is converted to nitrogen. Some oxides of nitrogen are also formed in electrostatic precipitators (HSMO, 1992). Carbon dioxide and carbon monoxide are formed as main products of the combustion process.
Carbon monoxide is formed by the incomplete combustion of carbonaceous fuels and even with good combustion control small amounts of carbon monoxide will be present in combustion gases. The dissociation of limestone produces up to 0. 75 tonnes of carbon dioxide ([pic]) per tonne of quicklime, depending on the composition of the limestone and the degree of calcination. The amount of carbon dioxide produced by combustion depends on the chemical composition of the fuel and on the heat use per tonne of quicklime; generally it is in the range 0. 2–0. 5 tonnes [pic] per tonne of quicklime (European Commission, 2001). The heat of dissociation of calcium limestone is 3,200 MJ/tonne. The net heat use per tonne of quicklime varies considerably with kiln design. Rotary kilns generally require more heat than shaft kilns. The heat use tends to increase as the degree of burning increases. The net heat use varies between 3,600 and 7,500 MJ/Mg of lime for calcium quicklime and light- and hard-burned dolomite, and between 6 500 and 10 500 MJ/Mg of lime for dead-burned dolomite (European Commission, 2001). 2. 3. 4 Controls
Emissions of sulphur oxide can be reduced by using low sulphur fuels and by limiting the sulphur contents of the fuel and raw materials. Sulphur dioxide emissions may be further reduced if the polluting equipment is fitted to desulphurise the exhaust gases (e. g. by using a wet process) (EPA, 1995; HMSO, 1992). The design of kiln and combustion conditions may be selected to ensure that most of the sulphur is retained in the burnt lime. In most circumstances, especially in shaft kilns, only a small fraction of the sulphur dioxide generated within the kiln (whether originating from the raw materials or rom the fuel) is released to atmosphere, since it is mainly incorporated into the lime by chemical combination (HSMO, 1992). The following techniques can be reasonably applied to reduce oxides of nitrogen discharges to the atmosphere: • The use of low-NOx-burners where practicable, which operate by avoiding localized hot spots. • The use of very finely pulverized coal so that complete combustion can be achieved with low excess air. Modern lime works are equipped with electrostatic precipitators that remove at least 98 % of the particulate matter from exhaust gases.
Other control devices are also used including multiple cyclones, wet scrubbers and bag houses. 2. 4. 0 Environmental, Health, and Safety Guidelines for Lime Manufacturing The Environmental, Health, and Safety (EHS) Guidelines are technical reference documents with general and industry specific examples of Good International Industry Practice (GIIP) when one or more members of the World Bank Group are involved in a project, these EHS Guidelines are applied as required by their respective policies and standards.
These industry sector EHS guidelines are designed to be used together with the General EHS Guidelines document, which provides guidance to users on common EHS issues potentially applicable to all industry sectors. Recommendations for the management of EHS issues common to most large industrial facilities during the construction and decommissioning phases are provided in the General EHS Guidelines. 2. 4. 1 Environment Environmental issues in lime manufacturing projects primarily include the following: • Air Emissions • Energy consumption and fuels Wastewater • Solid waste generation • Noise 2. 4. 1. 1 Air Emissions Air emissions in lime manufacturing are generated by the handling and storage of intermediate and final materials, and by the operation of kiln systems, and mills. For lime manufacture, there are 4 basic types of kilns used to produce different types (reactivity) of quicklime: rotary, shaft vertical (more than 10 types), traveling grate, and gas Suspension calcination. Exhaust Gases Combustion sources for power generation are common in this industry sector.
Guidance for the management of small combustion source emissions with a capacity of up to 50 megawatt hours thermal (MWth), including air emission standards for exhaust emissions, is provided in the General EHS Guidelines. Guidance applicable to emissions sources greater than 50 MWth are presented in the EHS Guidelines for Thermal Power. Particulate matter Particulate matter (PM) emissions are among the most significant impacts of lime manufacturing. The main sources of PM emissions and their respective recommended prevention and control methods include the following, as below.
For PM emissions associated with intermediate and final materials handling and storage (including crushing and grinding of raw materials); handling and storage of solid fuels; transportation of materials (e. g. by trucks or conveyor belts), and bagging activities, the recommended pollution prevention and control techniques include the following: • Use of a simple, linear layout for materials handling operations to reduce the need for multiple transfer points; • Use of enclosed belt conveyors for materials transportation and emission controls at transfer points; •
Cleaning of return belts in the conveyor belt systems; • Storage of crushed and preblended raw materials in covered or closed bays; • Storage of pulverized coal and petroleum coke (pet–coke) in silos; • Storage of waste-derived fuels in areas protected from wind and other weather elements; • Storage of screened sizes of burnt lime in bunkers or silos and storage of fine grades of hydrated lime in sealed silos; • Implementation of routine plant maintenance and good housekeeping to keep small air leaks and spills to a minimum; • Conduct material handling (e. . crushing operations, raw milling, and grinding) in enclosed systems maintained under negative pressure by exhaust fans.
Collecting ventilation air and removing dust using cyclones and bag filters; Implementation of automatic bag filling and handling systems to the extent possible, including: o Using a rotary bag filling machine with automatic paper bag feeder and fugitive emission control o Using automatic weight control for each bag during discharge o Using conveyor belts for transporting bags to a palletizing machine Storing the finished pallets in covered bays for subsequent shipping For particulate matter emissions associated with the operation of kiln systems, , and mills, including limestone burning, the following pollution prevention and control techniques, in addition to proper smoothing of kiln operations, are recommended: Developing a staged combustion process, as applicable in preheater-precalciner (PHP) and preheater (PH) kilns; · Lime manufacturing: Nitrogen oxide ([pic]) production is generally lower in lime manufacturing than in cement manufacturing. Because limestone burning usually takes place at lower temperatures, ([pic]) emissions from this source are lower and can be controlled using low NOX burners. Sulfur Dioxides
Recommended pollution control techniques for reduction of [pic], in addition to proper smoothing of kiln operations, include the following: • Use of a vertical mill and gases passing through the mill to recover energy and to reduce the sulfur content in the gas. In the mill, the gas containing sulfur oxide mixes with the calcium carbonate (Ca[pic]) of the raw meal and produces calcium sulfate (gypsum); • Selection of fuel source with lower sulfur content; • Injection of absorbents such as hydrated lime (Ca [pic]), calcium oxide (CaO), or fly ashes with high CaO content into the exhaust gas before filters; • Use of wet or dry scrubbers. pic] Emissions in lime manufacturing are generally lower than in cement because of the lower sulfur content of raw materials. • Techniques to limit [pic] emissions include the following: Selection of quarried materials with lower volatile sulfur content; • Injection of hydrated lime or bicarbonate into the exhausted gas stream prior to use of filters; • Injection of finely divided quick or hydrated lime into the firing hood of the kiln. Greenhouse gases Greenhouse gas emissions, especially carbon dioxide ( [pic]), are mainly associated with fuel combustion and with the decarbonation of limestone, which in its pure form is 44 percent [pic] by weight.
Recommended techniques for [pic] emission prevention and control, in addition to proper smoothing of kiln operations, include the following: • Process selection and operation to promote energy efficiency (dry/ pre-heater / pre-calciner); • Selection of fuel with a lower ratio of carbon content to calorific value (e. g. natural gas, fuel oil, or some waste fuel); • Selection of raw materials with lower organic matter content. Carbon monoxide ([pic]) makes a minor contribution to greenhouse gas emissions (less than 0. 5–1 percent of total emitted gases). These emissions are normally related to the organic matter content of the raw material. Additional recommendations for the management of GHGs are provided in the General EHS Guidelines. Waste fuels
Kilns, due to their strongly alkaline atmospheres and high flame temperatures (200°C), are capable of using high calorific value waste fuels (e. g. used solvents, waste oil, used tires, waste plastics, and organic chemical waste including Polychlorinated biphenyls [PCBs], obsolete organ chlorine pesticides, and other chlorinated materials). The use of waste fuel can lead to emissions of volatile organic compounds (VOCs), polychlorinated dibenzodioxins (PCDDs) and dibenzofurans (PCDFs), hydrogen fluoride (HF), hydrogen chloride (HCl), and toxic metals and their compounds if not properly controlled and operated. Use of waste fuel or waste raw material in cement manufacturing requires a specific permit from the local authority.
The permit should specify the amounts and types of waste that may be used either as fuel or as raw material, and it should also include quality standards such as minimum calorific value and maximum concentration levels of specific pollutants, such as PCB, chlorine, PAH, mercury, and other heavy metals. Recommended prevention and control techniques for these types of air pollutants include the following: Implementing PM abatement techniques to reduce nonvolatile heavy metals emissions and managing the captured waste materials as a hazardous waste as described in the General EHS Guidelines; o Implement monitoring and control of the volatile heavy metal content in the input materials and waste fuels though implementation of materials selection.
Depending on the type of volatile metals present in the flue gas, control options may include wet scrubbers and activated carbon adsorption; o Directly injecting fuels that have volatile metals or high VOC concentrations into the main burner rather than via the secondary burners; o Avoiding the use of fuels with high content of halogens during secondary firing and during startup and shutdown phases; o Keeping kiln gas cooling times (from 500 to 200°C) to a minimum to avoid or minimize the reformation of already destroyed PCDDs and PCDFs12, 13, 14; o Implementing proper storage and handling practices for hazardous and nonhazardous waste to be used as waste fuel or raw material, as described in the General EHS Guidelines. o Waste fuel and waste raw materials are seldom used in lime manufacturing because of product quality requirements 2. 4. 1. 2 Wastewater Industrial Process Wastewater Treatment Wastewater is generated mainly from utility operations for cooling purposes in different phases of the process (e. g. earings, kiln rings) Process wastewater with high pH and suspended solids may be generated in some operations. Techniques for treating industrial process wastewater in this sector include flow and load equalization with pH adjustment; sedimentation for suspended solids reduction using settling basins or clarifiers; multimedia filtration for reduction in nonsettleable suspended solids. Management of industrial wastewater and examples of treatment approaches are discussed in the General EHS Guidelines. Through use of these technologies and good practice techniques for wastewater management, facilities should meet the Guideline Values for wastewater discharge .
Other Wastewater Streams & Water Consumption Guidance on the management of non contaminated wastewater from utility operations, non-contaminated storm water, and sanitary sewage is provided in the General EHS Guidelines. Contaminated streams should be routed to the treatment system for industrial process wastewater. Storm water flowing through pet coke, coal, and waste material stockpiles exposed to the open air may become contaminated. Storm water should be prevented from contacting stockpiles by covering or enclosing stockpiles and by installing run-on controls. Recommended pollution prevention techniques for dust emissions from stockpiles of raw materials, coal, and waste may also help to minimize contamination of storm water.
If storm water does contact stockpiles, soil and groundwater should be protected from potential contamination by paving or otherwise lining the base of the stockpiles, installing run-off controls around them and collecting the storm water in a lined basin to allow particulate matter to settle before separation, control, and recycling or discharge. Further recommendations on managing contaminated storm water are provided in the General EHS Guidelines. Recommendations to reduce water consumption, especially where it may be a limited natural resource, are provided in the General EHS Guidelines. 2. 4. 1. 3 Solid Wastes Sources of solid waste in lime manufacturing include the kiln dust removed from the bypass flow and the stack, if it is not recycled in the process. Limited waste is generated from plant maintenance (e. g. used oil and scrap metal). Other waste materials may include alkali or chloride / fluoride containing dust buildup from the kiln. In lime production, dust, ff-specification quicklime, and hydrated lime are reused / recycled in selected commercial products (e. g. lime for construction uses, lime for soil stabilization, hydrated lime, and palletized products). Guidance on the management of hazardous and non-hazardous wastes is provided in the General EHS Guidelines. 2. 4. 1. 4 Noise Noise pollution is related to several lime manufacturing phases, including raw material extraction (discussed in the EHS Guidelines for Construction Materials Extraction); grinding and storage; raw material, intermediate and final product handling and transportation; and operation of exhaust fans. The General EHS Guidelines provides levels for recommended noise abatement measures and ambient noise levels.
The most significant occupational health and safety impacts occur during the operational phase of lime manufacturing projects and primarily include the following: • Dust • Heat • Noise and vibrations • Physical hazards • Radiation • Chemical hazards and other industrial hygiene issues 2. 4. 1. 5 Dust Exposure to fine particulates is associated with work in most of the dust-generating stages of lime manufacturing, but most notably from quarry operation (see EHS Guidelines for Construction Material Extraction), and raw material handling. Exposure to active (crystalline) silica dust (SiO2), when present in the raw materials, is a relevant potential hazard in the lime manufacturing sector.
Methods to prevent and control exposure to dust include the following: • Control of dust through implementation of good housekeeping and maintenance; • Use of air–conditioned, closed cabins; • Use of dust extraction and recycling systems to remove dust from work areas, especially in grinding mills; • Use of air ventilation (suction) in lime-bagging areas; · Use of PPE, as appropriate (e. g. masks and respirators) to address residual exposures following adoption of the above-referenced process and engineering controls; • Use of mobile vacuum cleaning systems to prevent dust buildup on paved areas; 2. 4. 1. 6 Heat The principal exposures to heat in this sector occur during operation and maintenance of kilns or other hot equipment, and through exothermic reactions in the lime-hydrating process.
Recommended prevention and control techniques include the following: • Shielding surfaces where workers’ proximity and close contact with hot equipment is expected, using personal protective equipment (PPE), as needed (e. g. insulated gloves and shoes); • Minimizing the work time required in high temperature environments by implementing shorter shifts at these locations; • Making available and using, as needed, air- or oxygen supplied respirators; • Implementing specific personal protection safety procedures in the lime-hydrating process to avoid potential exposure to exothermic reactions. 2. 4. 1. 7 Noise and Vibrations Exhaust fans and grinding mills are the main sources of noise and vibrations in lime plants.
Control of noise emissions may include the use of silencers for fans, room enclosures for mill operators, noise barriers, and, if noise cannot be reduced to acceptable levels, personal hearing protection, as described in the General EHS Guidelines 2. 4. 1. 8 Physical hazards Injuries during lime manufacturing operations are typically related to slips, trips, and falls; contact with falling / moving objects; and lifting / over-exertion. Other injuries may occur due to contact with, or capture in, moving machinery (e. g. dump trucks, front loaders, forklifts). Activities related to maintenance of equipment, including crushers, mills, mill separators, fans, coolers, and belt conveyors, represent a significant source of exposure to physical hazards. Management of these types of hazards is described in the General EHS Guidelines. 2. 4. 1. 9 Radiation
An X-ray station is sometimes used to continuously monitor the raw material mix on the belt conveyor feeding the raw mill. Operators of this equipment should be protected through the implementation of ionizing radiation protection measures as described in the General EHS Guidelines. 2. 4. 2. 0 Chemical Hazards and other Industrial Hygiene Issues The potential accidental contact with CaO / CaOH on skin / eyes / mucous membranes is a specific hazard in lime production plants that needs to be assessed, prevented, and mitigated through emergency procedures and equipment. The presence of moisture may result in burns. Facilities for immediate washing of the affected body surface should be available, including eyewash facilities where quicklime is handled.
The handling areas should be covered and enclosed, if possible, to avoid generation of a dust hazard. Additional guidance on the management of chemical hazards is presented in the General EHS Guidelines. (Environmental, Health, and Safety Guidelines-Cement and Lime Manufacturing, April 30, 2007) CHAPTER 3: METHODOLOGY 3. 0 Introduction This chapter summarizes the procedures used in the study. It involved Literature review, data collection and measurements, data analysis, and presentation which were used to achieve the above stated specific objectives of the study. 3. 1 Literature Review Previous works were looked at in order to identify possible gaps that needed to be bridged.
This involved a look at written literature about the methods used in lime burning and the working principle behind each method and how the methods can be improved to reduce the hazards they pose. This was done through reading of text books and any other relevant document such as research papers written on the subject of health, safety and environmental hazards in lime burning. Internet searches were used to get the literature about the subject of lime burning and the involved hazards, through comprehensive searching for information about already existing industries and the methods employed by these industries in the lime burning process. This provided a clear and elaborate understanding of the whole concept of health, safety and environmental hazards in the lime burning industry. 3. Data Collection The lime burning/ production process used was assessed from the sizing/crushing of the limestone to be fed into the kilns to the last process of bagging. Focus was put on the hazards involved in each of the processes by looking at issues like lime dust (PM),waste flue gases, temperatures of surfaces and their effect on the health and environment. The site visit showed the current equipment (tools) being used, the shortcomings of the current methods used, the possible hazards involved, what the people involved think about the current methods. This was done through direct observation and interviewing of the workers and managers. 3. Technical Description of the lime burning process/ flow line Each lime burning process from crushing/ sizing to bagging was looked at in detail in relation to the OHS practices. 3. 4 Identification of Hazards Hazards involved from each process were identified, this was done through observation and a review of the past accidents that had ever occurred at the place, interviewing of the workers and staff and also through comparing with the literature to be able to generate the long term effects. 3. 5 Risk Assessment A risk assessment was carried out to rank the hazards. This was based on severity and frequency of occurrence. 3. 6 Data Analysis
After all the data had been collected from both the relevant literature and the site, it was carefully analyzed. Comparison of findings was done with the actual data collected from the site to help in drawing up important recommendations & conclusions concerning the health, safety and environmental hazards in lime burning industry in Uganda. This final analysis helped in coming up with a well documented, baseline study of the hazards in Lime burning. The level of compliance or discrepancy was sketched in form of graphs. Contributions to the health, safety and environmental hazards were also postulated in form of charts. 3. 7 Documentation A detailed documentation, giving an account of the work to be done in this whole project Milestones The researcher faced financial constraints, being a student he needed to raise money to carry out the study and inspection after taking long trips which was costly. Requests were however made to different people including friends and family members from whom some funds were solicited in order to carry out the research successfully. • The researcher also faced a problem of language barrier since most of the workers at Nomson Lime Limited spoke and understood a different language (Swahili) which the researcher did not understand so well, so this hindered communication with some of the vital people. • The researcher also faced a problem of bias.
Most of the employees at Nomson were so biased in their responses due to the fear that the researcher could use the information against them at some point; this was a very big hindrance since the researcher kept getting conflicting responses. • Lack of proper measuring tools to carry out the required measurements of flue gas emissions and particulates. This hindered the generation of an experimental investigation of the lime burning process. CHAPTER FOUR: Results and Discussions This chapter presents the results and discussions of the study that was conducted at Nomson Lime Limited. These findings include the full description of the lime burning process and hazards involved at each of the stages, together with available remedies. The critical accidents that have ever occurred at the site have also been discussed. 4. 1 Technical Description of the Lime burning process:
At Nomson lime Limited, the raw material used for the production of lime is calcium Carbonate (CaCO3) or commonly known as Limestone. 4. 1. 1 Crushing the stones Sledge hammers are used to excavate the limestone from the quarry at Usukuru hills complex which is then transported to the plant by use of trucks. At the plant, manual crushing of the limestone to about 4 inch size takes place using ball pene hammers. The fuel used at Nomson is firewood. 4. 1. 2 Charging of the kilns The wood logs are manually pushed to the kiln. A first layer of firewood of 1. 5 meters from the bottom is then loaded into the kiln. This is then followed by an alternate layer of the crushed limestone occupying 1 meter.
Firewood logs occupying 1 meter are then added on to the stones followed by a 1 meter later of fresh stones forming a hip that covers the firewood logs at the top of the kiln. 4. 1. 3 Calcinations The fire is lit through one of the doors of the kiln and the burning process starts, this is left to go on for some time, and approximately six hours. By this time, the kiln has sunk to about 2. 5meters. Rejects and fire logs are then added to fill up the kiln while leaving the burning process to continue up to when the level sinks to 1 meter. Firewood logs and fresh limestone are added to fill up the 1 meter and leaving the burning process to proceed. Abundant time is then left up to when the kiln level drops by 0. 5 meters. This is followed by the last addition of firewood logs and rejects.
The kiln is then left to burn and cool for the next 3 days. CaCO3 + heat > CaO + CO2 (high calcium lime) 4. 1. 4 Offloading The quicklime from the kiln is extracted through the door using spades and transported manually to the hydration area by wheel barrows. It takes a total of 3 days to offload the kiln. 4. 1. 5 Hydration The offloaded quicklime is spread on the ground in a shade to a level of 1 meter. This is followed by pouring water on to the quicklime using jerry cans after which it is left to lie for 2 days before screening. During hydration, the quicklime lumps disintegrate to a fine powder. 4. 1. 6 Sieving After hydration, the material is then screened through 2 rectangular meshes.
Screening is done twice starting with a mesh with bigger holes and then followed by screening using the mesh with the smaller sizes. The material that cannot pass through the mesh is pilled and spread on the floor for further rehydration . After re-hydration, the material is screened again to extract more lime from it only leaving rejects thereafter. 4. 1. 7 Grinding The sieved lime is then ground in order to improve on its quality. 4. 1. 8 Bagging/ packing The ground lime is then manually packed in multilayer paper bags of 25 kgs. Block diagram showing the whole process REJECTS LIMESTONE Rejects FUEL Figure 3: process scheme for Lime burning Process Flow Chart at Nomson Lime Limited NO (REJECTS) YES figure 4
Figure 4: process flowchart for Lime burning 4. 2 Identification of Health, safety and Environmental hazards The lime burning process right from the manual crushing to the packaging/bagging was assessed, looking out for the possible hazards involved. Questionnaires, direct interviews were some of the tools that were used to collect the necessary information regarding the health, safety and environmental hazards in lime burning at Nomson lime limited. Each process together with the underlying events and outcomes (short and long term outcomes) have been given in the table below. Table 1: Lime burning processes, events and their respective outcomes. PROCESS |HAZARD |OUTCOME | |Crushing |Sharp stone edges |hit the workers | | |The tiny particles that come off stones |workers feet at risk since most are bare footed | | | |roughening of hands/ palms | | | |Inhalation of dust particles | | | |Irritation to the eyes, nose and throat, liver damage, and damage to the nervous system | | | | | |Charging the kiln |Heavy logs that are manually carried/ pushed |great risk to the worker’s backs and hests | | |poor loading and construction of kilns |Being hit by heavy firewood logs | | | |Accidents due to collapse of kilns | |Calcinations |Excessive heat(mean wall temperature of kiln was found to |abundant heat penetrating the worker’s bodies (no gadgets) | | |be 377. 05OC) |inhalation of the smoke | | |Uncontrolled emissions (Toxic effluent releases) |Various pollutants released to the environment | | |smoke? aden atmospheres |Climate change | | |Lime Kiln Dust |Eyes Contact can cause severe irritation or burning of eyes, including permanent damage. | | | |Skin Contact can cause severe irritation or burning of skin, especially in the presence of moisture | |Offloading |spade is used to carry the quicklime from kiln(no gadget) |Worker at risk of burns( No proper safety gadgets) | | |Excessive heat |Potential damage to the skin. | |Too much dust evolves from the kiln which is inhaled |inhalation of the particulates | | | |Occupation skin diseases (irritant contact dermatitis, and allergic contact dermatitis) | | | |Lime kiln dust may contain trace amounts of crystalline silica in the form of quartz or crystobalite, which has | | | |been classified by IARC as a Group I carcinogen to humans when inhaled.
Inhalation of silica can also cause a | | | |chronic lung disorder, silicosis | |Hydration |Inhalation of dust particles |Inhalation of toxic particulates | | |Abundant heat evolve from the operation (hydration |Occupation skin diseases (irritant contact dermatitis, and allergic contact dermatitis) | | |temperature of 123 OC ) |Irritation to the eyes, nose and throat, liver damage, and damage to the nervous system | | | |Occupational lung diseases (occupational asthma) | | | |Skin and eye irritation | | | |Eye damage | | | |Bronchitis | | | |Skin/lung cancer | | | |Ingestion can cause severe irritation or burning of gastrointestinal tract | | | |Inhalation of lime dust can cause severe irritation of the respiratory system. Long-term exposure may cause | | | |permanent damage | | | |This material is alkaline and if released into water or moist soil will cause an increase in pH. | |Sieving |dust fumes pread into the workplace |Very dangerous to human health(inhalation) and the environment | | | |Potential damage to body organs (no proper safety gadgets) | | | |Occupation skin diseases (irritant contact dermatitis, and allergic contact dermatitis) | | |