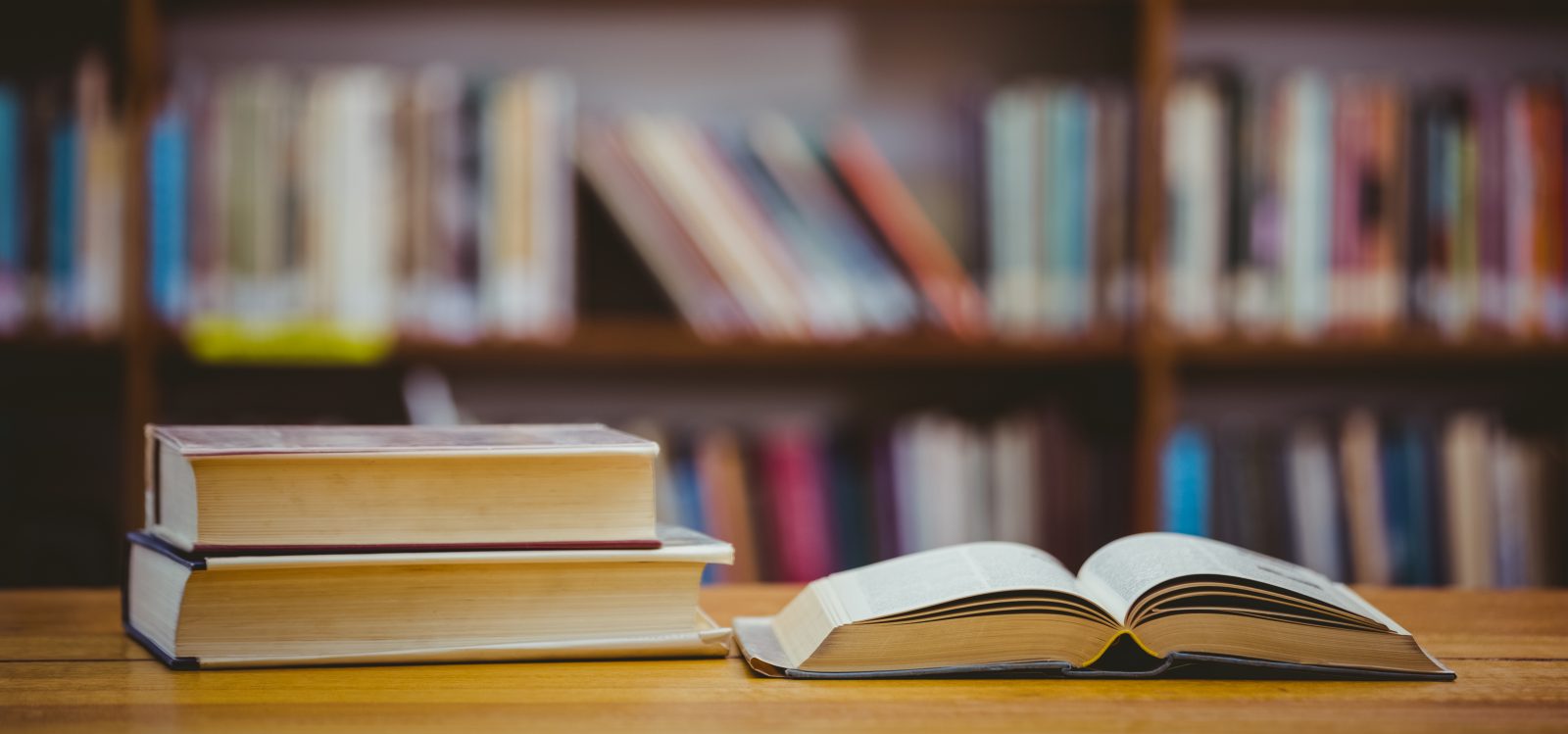
Microbot based Desktop Manufacturing System Ajil Philip Mammen Enterprise Systems Center, 200 Mohler Lab, Bethlehem, PA-18015, USA Tel: 610-803-5093| Email: apm210@lehigh. edu Abstract A microfactory is a concept that has been around for many years. Microfactories generally refer to small factories able to produce small products. Traditional microfactories conserve space and energy and reduce operational costs and investment. However this system is limited in its ability to be reconfigured and not very mobile or agile.
In this report we discuss a heterogeneous swarm micro-robot based microfactory, the components that make up the robots and most importantly the control systems that need to be implemented for satisfactory coordinated working of the system. This system will be highly mobile and very easy to reconfigure thus overcoming some of the difficulties facing traditional micromanufacturing. It also discusses a case study of a robot based micromachining factory and future tasks and challenges for the system. * Introduction & Overview
In the fields of high precision & nano-manufacturing there is a need for discretization of manufacturing facilities i. e. moving away from large scale flow line production of generic products to small batch or one-off products. This has given birth to the term “micro-factory”. The Mechanical Engineering Laboratory (MEL) of Japan defines a micro-factory as “A small-size production system suitable for fabricating small size-products”. A micro-factory provides high customizability and allows us to move production closer to areas of consumption reducing requirements of transportation and inventory.
Conventional methods cannot accomplish these functions especially if the product variety is high. Okazaki et. al [ (1) ] defined the basic advantages of using a micro-factory based manufacturing system: 1. General Environmental Aspects: i. Saving energy and material resources ii. Reduced vibration and noise for workers and the factories’ neighbors iii. Easier control of waste and pollution 2) Economic Aspects i. Reduced need for capital investment in the machinery itself and facilities such as land space, buildings, power sources, environmental conditioning, etc. i. Reduced running costs such as energy consumption, facility maintenance, air conditioning, clean-room operation, etc. iii. Efficient utilization of space: More machinery can fit in less space iv. Improved portability and agile recon? gurability: Easier replacement of machinery and dynamic recon? gurability of the shop ? oor in response to the changing demands of variable-product/variable-quantity manufacturing. v. Ubiquitous manufacturing: The manufacturing site can move off the conventional factory ? oor 3) Technical and Engineering Aspects i.
Precision: Freedom of configuration and proportion in machine design will increase. ii. Productivity: Productivity can be increased by the dense and highly parallel allocation of machinery. iii. User-oriented machine design: Modular design of machines can easily be realized, and the machines can be reconfigured with ease However in a micro-factory the issues are material handling and the inability for the machines to work on objects larger than the machines themselves. For this purpose using miniature robots with the practical characteristics of micro functions is a good solution.
They have the potential to perform accurate and fine operations with great cost saving benefits at the multiple scales down to the nanometric level. [ (2) ] Conventional Desktop Factory (courtesy Sankyo Seikei) The issues with small robots are the low mobility and inability to perform complex tasks since they have poor capacity of loading space and driving force. Thus the solution for this issue is usage of multiple micro robots with specific tasks working according to a collaborative behavior scheme i. e. working serial, parallel or mixed depending on the task at hand or the discretion of the programmer.
The following are the basic requirements of a micro-robot for use in manufacturing: i. Must behave in a deliberate manner ii. Must react appropriately to its environment iii. Must anticipate uncertain information iv. Must be both robust and fault tolerant v. Architecture must be incrementally flexible Using Swarm Robotic technology we can have multiple robots incorporating actuation devices, sensors and feedback systems in association with a suitable control system to perform together as a desktop manufacturing workstation or micro-factory. (3, 4) ] Micro-factories are needed for the improvement of manufacturing techniques. They will aid in creating innovative processing techniques, processing equipment development and production systems. Swarm robotics is an approach to the coordination of multirobot systems which consist of large numbers of mostly simple physical robots. It originated from the biological studies of ants, bees and other insects which exhibit swarm behavior. In order to manage the many small robots in a swarm there is a requirement for a system to plan, schedule and control them using multiple local and global feedback loops.
For a smart manufacturing system we need to combine swarm robots and intelligent systems. Beni defines an intelligent robot as “A robot whose behavior in response to a change in the environment external to the robot is neither random nor predictable. ” As an amalgamation of these two concepts, Swarm intelligence consists of systems of non-intelligent robots exhibiting collectively intelligent behavior in the ability to unpredictably produce specific ordered patterns of matter in the external environment.
An intelligent swarm can be used as a constructor, a system to create patterns of some kind of ordered structures either internally, as self organization, or externally like self reproduction. [ (5) ] * System Requirements The micro-robot swarm should be able to perform material synthesis and component assembly, concurrently. The micro-robots could be designed to perform basic operations such as pick and place, dispense liquids, print inks, remove material, join components, etc. These micro-robots should be able to move cooperatively within a workspace to achieve highly efficient synthesis and assembly.
This behavior should be programmable, in particular, the micro-robotic behavior should be more adaptive as the ability for real-time in-situ sensing increases. Examples of complex material systems of potential interest include but are not limited to: multi-functional materials, programmable materials, metamorphic materials, extreme materials, heterogeneous materials, synthetic materials, etc. [ (6) ] * System Architecture For meeting the above requirements, a four-layer architecture is suggested as used by Trifa et. al (7). It consists of: i.
Physical layer, consisting of the actual robots; ii. Gateway layer, which is the connection between the physical devices and the system; iii. Logic layer, containing the server that logs the data coming from the devices; iv. Interface layer, which includes any device or interface for an external user or users. Microrobots can be pooled together to do simultaneous actions using different tools, e. g. transferring, adjusting or gripping of objects. According to the task to be solved, the robots may work on an XY-stage mounted under a light microscope.
The microscope and the microrobots are controlled by a parallel control system which is equipped with several interface cards, power electronics and AD-converters. There is visual and force sensor feedback in the physcial layer. The central computer is used for task-specific assembly planning and offers a graphical user interface (GUI) with a tele- manipulation interface. With the help of the assembly planning system, the operational steps are defined, and then the corresponding commands are handed down to the control computer where they are resolved into a defined instruction sequence to activate the microrobots. (8-10) ] An assembly problem is specified in a parts description language or a CAD model to the interface layer. The control system located in the logic layer has to perform task planning, generate a motion sequence and control the execution of this sequence. * Design of Micro-robots * Power Supply Speaking of autonomous, highly miniaturized robots, the first limitation to be considered is the amount of available on-board energy. It also becomes clear that the amount of energy available on the robots is crucial while being a function of the robot’s size.
For some solutions, it depends only on its surface, for others on the available volume. There are many ways of providing power to the micro-robot but the most basic constraint is the avoidance of any physical connectors to an external power supply. There are multiple ways to power an autonomous micro-robot without physical connections * Rechargeable Batteries Rechargeable batteries have low initial cost compared to other solutions and are easily available but the disadvantage is the inability for continuous operations. These will have to be charged at regular intervals to keep them running.
There are many rechargeable battery solutions available in the market such as Lithium-Ion, Nickel Metal Hydride and traditional alkaline and sealed lead acid batteries. Li-Ion batteries have the highest power density among rechargeable battery packs and thus will have the smallest dimensions for a given output. The small relative size will makes it suitable for the constrained dimensions of a micro-robot. One of the most promising emerging concepts is the battery ultra-capacitor hybrid using Barium-Titanate powders from Eestor Technologies. The battery has 10x power density of present Li-ion batteries * Inductive Charging
Inductive charging uses the electromagnetic field to transfer energy between two objects. A charging station sends energy through inductive coupling to the electrical device. It is a kind of short-distance wireless energy transfer. Tseng et. al [ (11) ] demonstrated that a moving electric vehicle could be powered by inductive charging. Thus we do not require any battery pack on board the robots, only the charging setup needs to be on the robot. This will allow for major reduction in size and weight of the robot. The manufacturing desktop or floor can double up as an inductive charging surface on which operations take place. Actuators Most micro-actuators are based on electrostatic and electromagnetic principles. Ideal actuators for microrobotic applications should have reasonable speed, high torque and long strokes. Though some actuators like piezoelectric and electrostatic have a short stroke they are adequately compensated for by a high resonant frequency. [ (12) ] * Electric Field Driven actuators Polysilicon Scratch Drive Actuator coutesy Akiyama et. al Among the many novel devices of this kind are planar rotary micromotors and dielectric induction motors.
The drawback to them is the low force and torque obtained. For example the electrostatically driven gripper able to handle 10? m parts [ (13) ] has a grasping force of the order of 1? N, while the electrostatic micromotor has a diameter of 100? m and a torque of only 100pNm which is extremely low. However with newer materials and technology such as the double walled Carbon Nanotube Nanoactuator. (14) Electrostatic actuators have also been fabricated out of polysilicon and polyimide which can act out of the plane of the wafer and have multi-DOF.
These are being used to emulate insect joints and muscles. (15) In a Scratch Drive Actuator (SDA), the actuator sits on top of a substrate that has a thin insulating dielectric layer on top. A voltage is applied between the actuator and the substrate and the resulting potential pulls the body of the actuator downwards. When this occurs, the brush is pushed forwards by a small amount and energy is stored in the strained actuator. When the voltage is removed, the actuator springs back into shape while the bushing remains in its new position.
By applying a pulsed voltage, the SDA can be made to move forward. The SEM photograph of a polysilicon SDA by Akiyama (16) shows the device on an insulator film passivated on a substrate surface. Dielectric Electroactive polymer actuator Electroactive polymer actuators are another kind of electrostatic actuator which can be easily manufactured into different shapes and sizes just like traditional polymers. The Artificial Muscle Research Institute pioneered the use of ion-exchange polymer metal composites (IPMC) (17) as biomimetic sensors and actuators.
Strips of these composites can undergo large bending and flapping displacement if an electric field is imposed across their thickness. Thus, in this sense they are large motion actuators. Conversely by bending the composite strip, either quasi-statically or dynamically, a voltage is produced across the thickness of the strip. * Piezoelectric actuators Though piezoelectric actuators have a very short stroke, they have a very high operating frequency, which together can give us reasonable displacement. A major advantage of the short stroke is the high resolution which we can achieve provided we have a suitable control system.
SPIDER-II is a complete micro-manipulation robot capable of handling microscopic objects and moving over long distances. The robot includes six legs and a manipulator, driven by bimorphic piezoactuators with a voltage of ±60V. (18) Short stroke piezoelectric actuators can be amplified by suitable means to achieve greater displacement. APA™ from Cedrat Technologies uses an elliptic shell to amplify the strain. The amplification ratio can typically reach 20 times, which means these actuators can reach strokes of up to 1mm. * Magnetic Field Driven Actuators
A major advantage of electromagnetic actuation is the large displacement obtained with moderate force levels. Electrostatic drives also cannot work in conductive fluids such as water. One of the most significant drawbacks to (non-superconducting) magnetic actuators is the thermal dissipation in coils while maintaining a constant force, which is not an issue in electrostatic actuators which require no power to maintain a constant force with no displacement. * Sensors A sensor is a device that measures a physical quantity and converts it into a signal which can be read by an observer or by an instrument.
Technological progress allows more and more sensors to be manufactured on a microscopic scale as micro sensors using MEMS technology. In most cases, a micro sensor reaches a significantly higher speed and sensitivity compared with macroscopic approaches. * IR Bump sensors iRobot Roomba Infrared bump sensors are very common and inexpensive for use in autonomous robotic applications. iRobot®’s home cleaning robots such as the Roomba® (vacuum robot), Scooba® (floor washing robot), Verro® (pool cleaning robot) and Looj® (gutter cleaning robot) use infrared bump sensors to detect walls, furniture and other obstacles in the house.
The Create® educational robots from the same firm have modular designs and can be outfitted with Bluetooth®, Wi-Fi and Light sensors and can be programmed to behave collectively as a storm. * iPhone 4 STMicroelectronics AGD1 3-Axis Gyroscope (highly magnified) Inertia Sensor An inertia sensor or an accelerometer is also very commonly used and deployed in devices from cell phones to automobile airbag deployment systems. These are very sensitive and can be configured for a variety of purposes. VTI’s CMA3000 series of 3-axis accelerometers are now available in sizes as small as 2x2x0. 95mm3 and can work with sub-10?
A current consumption. The STMicroelectronics AGD1 3-Axis Gyroscope in Figure 5 is manufactured by the THELMA (Thick Epi-Poly Layer for Microactuators and Accelerometers) process which is based on surface micromachining of a deposited polysilicon layer on a sacrificial oxide using “Bosch-Style” deep reactive ion etching. * Acoustic Wave Sensor The telecommunications industry is the largest user of Acoustic wave sensors primarily for mobile phones and base stations. These are typically surface acoustic wave (SAW) devices, and act as bandpass filters in both the RF and IF sections of the transceiver electronics.
Newer applications for these devices include automotive (non-contact tyre pressure and torque sensors) and medical (biosensor) applications. [ (19) ] Parallax Ping))) acoustic sensor Parallax’s PING)))™ ultrasonic sensor provides a very low-cost and easy method of distance measurement. This sensor is perfect for any number of applications that require you to perform measurements between moving or stationary objects. The Ping sensor is an active sensor i. e. it transmits as well as receives acoustic signals. It provides precise, non-contact distance easurements within a 2 cm range. * * Communication Systems Communication in the system, be it host-to-robot or robot-to-robot is essential to the working of the system. The principles which could be employed for communication are the following: Comparison of Communication Systems Of these available technologies only the ones most suited for use in highly compact, low power systems with low system power usage are discussed. * Zigbee ZigBee is a specification for a suite of high level communication protocols using small, low-power digital radios based on the IEEE 802. 5. 4-2003 standard for Low-Rate Wireless Personal Area Networks (LR-WPANs)(20). Its advantages are the low cost and the very low power requirements. There are two physical device types in ZigBee: i. Full Function Device (FFD): These can function in any topology and act as network coordinators. They can communicate in any direction i. e. to hosts, other coordinators and those lower on the communication hierarchy ii. Reduced Function Device (RFD): These can function only in the star topology with the centre of the star being a network coordinator.
RFD’s can only communicate with their network coordinators A ZigBee network requires at least one full function device as a network coordinator, but endpoint devices may be reduced functionality devices to reduce system cost. With a suitable network of FFD’s and RFD’s we can communicate among the entire network at high speed with low usage of resources. * Bluetooth Bluetooth is a proprietary open wireless technology standard for exchanging data over short distances (using short wavelength radio transmissions) from fixed and mobile devices, creating personal area networks (PANs) with high levels of security.
Bluetooth is a mature technology with well established protocols and is highly suited for wireless networking. The issue with Bluetooth is the relatively higher power consumption compared to technology like ZigBee. * Control Systems The controller is the robot’s brain and controls the robot’s movements. It’s usually a computer of some type which is used to store information about the robot and the work environment and to store and execute programs which operate the robot. The control system contains programs, data algorithms, logic analysis and various other processing activities which enable the robot to perform.
Autonomous robots are programmed to understand their environment and take independent action based on the knowledge they possess. Shen et. al (21) has presented the Digital Hormone Model (DHM) as a bio-inspired control method for robot swarms and self-organization. The robots are viewed as biological cells that communicate and collaborate via hormones and execute local actions via receptors. The DHM model’s drawback is that it views the swarm as a network of identical robots that can dynamically change their links in a network. The hormone-like messages do not have addresses but propagate throughout the swarm.
This approach is usable for a swarm in which all the robots are identical but for the purposes of a micro-factory we require different robots that can perform different tasks. Combining purely reactive control with other control mechanisms like PID controllers, fuzzy logic or Artificial Neural Networks leads to a more complex and usable way of controlling swarm robots like the Jasmine MDL2? based Operating System (JaMOS). It combines data acquisition and processing with robot control in an easily exchangeable manner. The issue with most of the above control systems is that they are for homogenous robot systems i. . for systems in which all the robots are the same, their positions and roles in the system are interchangeable. In a micro-manufacturing system we will have robots that are unique, each with different end effectors and actuators, each performing a different function. For such a system Trifa et. al (7) suggested the dynamic control system using a service-oriented architecture. In this approach the logic layer consists of a J2EE based set of instructions which are executed based on input received from the robots and the requirements set out by the human controller with each individual working within constraints (e. . Mechanical, physical) which are defined in the database. The database has two functions: i. It is a repository of the capabilities of each member thus instructions are assigned keeping them in mind. ii. It is used to store operation & operator relationships i. e. how operations can precede or follow each other. For e. g. work piece must be centered on a lathe before turning. * Sequence Planning Sequence planning includes three major issues: i. Product design representation ii. Sequence generation iii. Allocation of single operations.
A product design consists of assembly sketches and provides information about part geometry, relations between the parts, bill of materials, etc. The information of contact and fitting relationships between the parts must be defined for different directions, and is also used by the operation sequence generation algorithm. The sequence is generated based upon the feasibility of operations (capabilities of robot etc. ) which is defined in the World Model of the database. The entire operation can be condensed into the following five steps as described by Mardanov et. l [ (22) ] i. The user describes the product of the assembly by describing its parts according to product models stored in the database with the help of product design tools. The information about final product can be taken from product planning stage or can be specified by user. ii. A relations analyzer uses the assembly description structures to automatically determine assembly liaisons in terms of freedom of separation of parts. iii. The assembly planner uses structures which define assembly relationships to generate assembly sequences and determine their feasibility.
The sequences will be analysed in terms of cost of operations to find an optimal one. The sequences will be allocated for single operations by the execution planner, which produces robot control language code used by the interpreter. iv. The interpreter will rearrange particular commands to corresponding procedures and functions of control algorithms. v. The robot commands will be executed in the micro station with previously prepared micromechanical components and devices under vision-based control algorithms . Flowchart for Operations Case Study: Automatic Drilling by Multiple Micro Robots The Applied Microsystems Lab at the University of Electro-Communications, Tokyo, Japan demonstrated the concept by implementing Swarm Control for Automatic Drilling by Multiple Micro Robots [ (23) ]. An automatic drilling system employing several piezoelectric driven miniature robots for transporting the target work piece, holding the micro drill and cooperating to drive it was developed. The micro robots consist of a pair of piezo-elements for locomotion and electromagnets for surface clamping and provide sub-micron level positioning resolution.
This arrangement allows the robot to move on vertical walls and ceilings as well though the target surface is limited to a ferromagnetic material. * Components * Micro Drill with reduction gear This is a small robot which has a micro drill with reduction gear on the axis. Here small drills with diameters of 0. 5mm to 0. 05mm can be supported by the simple bearing unit on the main body with the reduction gear attaching to the main shaft. The large gear is for power transmission as well as for providing multi-point gear contacts in any direction.
This robot can move around the reduction gear with the drill bit for positioning and also integrate the power transmission. * Microdrill with reduction gear * Micro motor with pinion gear and microphones Microdrill with DC motor & microphone This is a small robot incorporated with a micro pinion geared DC motor and a pair of microphones. When the buzzer is active, then the differential signal from the two microphones is used for switching each piezo actuator. This allows the robot to navigate using the sound signal source.
The purpose of this robot is to provide navigational control to the whole system since other robots will align with it using the reduction gear system. * Sample Holder The small robot with the sample holder can move up and down on the vertical wall for transporting the work piece onto the drill top and feeding it carefully. Small optical reflectors are also attached in order to identify the heading direction of the robot and the centre point with respect to the drill axis using the visual monitoring camera. * Control System
This figure shows the control system where several micro-robots with tools, CCD camera monitoring instruments, frame image processor and computational facilities are organized. Using a computer with fast real time image processing instruments it is possible to provide high resolutions over the entire vision area. The coordinate positions of each robot with an accuracy of about 0. 1mm can be achieved. The small robots with micro DC motor are maneuvered using an acoustic signal based navigation system. It uses 1kHz sound signal generated by a buzzer on the reduction gear robot which is then used by the robot with microphones to home in towards. * Micro Robot Drilling control scheme Conclusion Using the setup described many thin holes of down to 0. 05mm have been machined automatically by the multiple micro robot system. The issues faced by the system are the deviation of the small robots from the assigned path and deadlocking of acoustic homing robots when in contact with each other. However these can be resolved with more accurate coordinate measuring instruments and controls for dead lock recovery Micro drilled work piece * * Future Work * The European Commission is funding the I-Swarm project at the Universitat Karlsruhe, Germany.
The goal of the project is to build a very large scale artificial swarm (VLSAS) with a swarm size of up to 1000 micro bots with a planned size of 2x2x1 mm3. The applications of this project are seen in micro assembly, biological, medical or cleaning tasks. [ (24) ] CAD drawing of I-Swarm robot * Material transport by Microbacteria Flagellated magnetotactic bacteria are being used for assembly of simple micro-structures. In an experiment by Martel & Mohammed [ (25) ] 5000 bacteria were involved in the construction of a miniature step pyramid. It was a computer controlled process and the whole procedure was completed in 15 minutes.
With further research micro-robots might become completely obsolete in micro-assembly systems and be replaced by biological equivalents Conclusion Thus it has been how micro robots can be used for manufacturing of components and parts much larger than them using a coordinated swarm approach and appropriate control systems. We have seen the parts and components that can be used for the creation of such microrobots and suitable control systems for their optimal operation. Heterogeneous swarms can be used to perform tasks that are complex for traditional homogenous swarm systems.
The next natural steps in this progression would be the self replication of the robots in order to adapt to changes in scale of operational requirements and conditions. There are many moral and ethical issues associated with micro & nano scale swarm robots and these need to be tackled before mass manufacturing of such systems can take place. This approach holds great promise for the manufacturing systems of tomorrow and with greater precision in micro fabrication robots will only get smaller and be able to perform more functions than before. * References 1. Okazaki Y, Mishima N, Ashida K. Microfactory—Concept, history, and developments.
Journal of Manufacturing Science and Engineering. 2004 November 2004;126:837-44. 2. Aoyama H, Nakano H, Hayakawa N, Sasaki A, Shimokohbe A. Miniature robots for ultra precision measurement and machining. Proc of 7th Intl Conf on Prec Engg Semr. 1993:275-89. 3. Doring K, Petersen HG. In: Multi-robot task scheduling in micro-manufacturing. Assembly and task planning: From nano to macro assembly and manufacturing, 2005. (ISATP 2005). the 6th IEEE international symposium on; ; 2005. p. 125-31. 4. Doty KL, Van Aken RE. In: Swarm robot materials handling paradigm for a manufacturing workcell. Robotics and automation, 1993. roceedings. , 1993 IEEE international conference on; ; 1993. p. 778,782 vol. 1. 5. Beni G, Spears WM, Sahin E. From swarm intelligence to swarm robotics. In: Swarm Robotics: Lecture Notes in Computer Science. Springer Berlin / Heidelberg; 2005. p. 1-9. 6. Desktop manufacturing with micro-robot swarm [Internet]. ; 2011. Available from: http://www. navysbir. com/n11_A/navst11-037. htm. 7. Trifa VM, Cianci CM, Guinard D. In: Dynamic control of a robotic swarm using a service-oriented architecture. January 31 – February 2, 2008. ; ; 2008. 8. Fatikow S, Mounassypov R. In: Assembly sequence planning for manufacturing by microrobots.
Assembly and task planning, 1997. ISATP 97. , 1997 IEEE international symposium on; ; 1997. p. 269-74. 9. Fatikow S, Mounassypov R. In: Microassembly planning for manufacturing by flexible microrobots. Robotics and automation, 1998. proceedings. 1998 IEEE international conference on; ; 1998. p. 3362,3367 vol. 4. 10. Fatikow S, Seyfried J, Fahlbusch S, Buerkle A, Schmoeckel F. In: A flexible microrobot-based microassembly station. Emerging technologies and factory automation, 1999. proceedings. ETFA ’99. 1999 7th IEEE international conference on; ; 1999. p. 397,406 vol. 1. 11. Tseng L, Tseng D, inventors; Tseng L, assignee.
Inductive charging of a moving electric vehicle’s battery. United States patent 5311973. 1994 May 17th, 1994. 12. Fearing RS. Powering 3 dimensional microrobots: Power density limitations. 1998 September 24th. 13. Ahn CH, Kim YJ, Allen MG. A planar variable reluctance magnetic micromotor with fully integrated stator and coils. Microelectromechanical Systems, Journal of. 1993;2(4):165-73. 14. Kuznetsov S, Lozovik Y, Popov A. The nanoactuator based on a carbon nanotube. Phy of the Sol Stat. 2006;49(5):1004-12. 15. Suzuki K, Shimoyama I, Miura H. Insect-model based microrobot with elastic hinges. Microelectromechanical Systems, Journal of. 994;3(1):4-9. 16. Akiyama T, Collard D, Fujita H. Scratch drive actuator with mechanical links for self-assembly of three-dimensional MEMS. Microelectromechanical Systems, Journal of. 1997;6(1):10-7. 17. Shahinpoor M. , Bar-Cohen Y, Xue T. , Harrison Joycelyn S. , Smith J. Ionic polymer-metal composites as biomimetic sensors and actuators-artificial muscles. In: Field Responsive Polymers. American Chemical Society; 1999. p. 25-50. 18. Fatikow S, Zollner J, Santa K, Zollner R, Haag A. In: Flexible piezoelectric micromanipulation robots for a microassembly desktop station. Advanced robotics, 1997. ICAR ’97. proceedings. 8th international conference on; ; 1997. p. 241-6. 19. Drafts B. Acoustic wave technology sensors. Microwave Theory and Techniques, IEEE Transactions on. 2001;49(4):795-802. 20. Baronti P, Pillai P, Chook VWC, Chessa S, Gotta A, Hu YF. Wireless sensor networks: A survey on the state of the art and the 802. 15. 4 and ZigBee standards. Comput Commun. 2007 5/26;30(7):1655-95. 21. Shen W, Will P, Galstyan A, Chuong C. Hormone-inspired self-organization and distributed control of robotic swarms. Autonomous Robots. 2004;17(1):93-105. 22. Mardanov A, Seyfried J, Fatikow S. An automated assembly system for a microassembly station.
Comput Ind. 1999 3;38(2):93-102. 23. Kuronita T, Tadokoro S, Aoyama H. In: Swarm control for automatic drilling operation by multiple micro robots. 14-15 November 2001; ; 2001. p. 7-12. 24. Seyfried J, Szymanski M, Bender N, EstaA±a R, Thiel M, WA¶rn H. The I-SWARM project: Intelligent small world autonomous robots for micro-manipulation. 2005;3342:70-83. 25. Martel S, Mohammadi M. In: Using a swarm of self-propelled natural microrobots in the form of flagellated bacteria to perform complex micro-assembly tasks. Robotics and automation (ICRA), 2010 IEEE international conference on; ; 2010. p. 500-5.